Atlas Brickworks, Bathville, Armadale, West Lothian.
Canmore
These works were situated directly East of the Etna Brickworks and they are the older of the two. It was started by Robert Fleming of Coatbridge and Mr Kopel Moritz.
Info
1882 – Fleming & Moritz, Brick and Tile Maker, Atlas and Armadale Brickworks, Bathgate.
05/01/1885 – Aberdeen Free Press – Aberdeen Town Council. Gasworks contract … The Gas Committee has accepted the following tenders for the supply of materials in connection with the undertaking for the ending 31st December 1885 … fire clay goods – Garnkirk Fire-Clay Company and J. & C. Grieve. The committee had also before them tenders for the lightning conductor, and for the supply of circle and header bricks for the new chimney stalk, and authorised the gas treasurer to accept the following: Bricks – Robert Fleming and Co. (Atlas or Calder Fire Clay Works?).
Below – 1886 – Robert Fleming & Co, Atlas Fire Brick Works.

04/02/1888 – Falkirk Herald – Action for damages – Thomas Crawford, farmer Bathville, Armadale raises an action for compensation for damages suffered in 1887 to his grass, turnip and stock upon his farm as caused by Robert Fleming & Co, Atlas Brickworks, Armadale. He wins the case and damages and expenses to the sum of £9 5s are awarded.
Below – 1889 – Robert Fleming and Co. Atlas Fire Brick Works, Calder and Carnbroe Brickworks.

1890 -91 – Atlas Fireclay Co, manufacturers of furnace blocks and fireclay bricks. Office Calder by Coatbridge. Works Calder, Carnbroe and Bathville.
1892 – 1895 – Invoices – Robert Fleming and Coy, Coatbridge. Atlas fire brick, furnace block, gas retort, chimney can and paving tile makers.
1892 – ? Office Calder.
? – 1894/1895. Office Carnbroe
1895 – ?. Office Bathville.
Below – 1893 – Advert – Robert Fleming Atlas Firebrick works Atlas Calder Carnbroe.
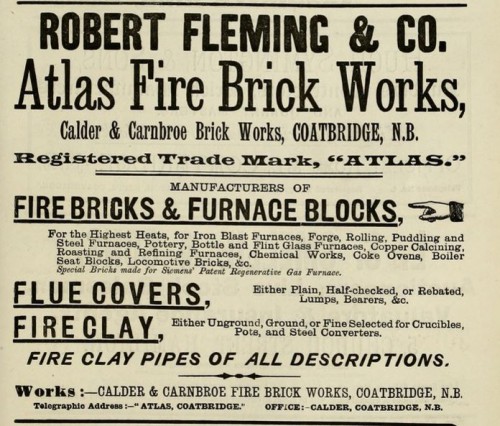
1893 – 1897 – Invoices – The Calder Fireclay Company by Coatbridge, fire brick, furnace block, gas retort, chimney can and paving tile makers. Office Calder. One dated 02/03/1893 is stamped in red along the top ” Late Robert Fleming and Co”.
1893 – 1894 – Fleming & Moritz, brick and tile manufacturers, Atlas and Armadale Brickworks. (Note – SBH – So which Mr Moritz was in partnership with Fleming? – Kopel Moritz died in 1889. If it was Kopels son Arthur then from the info above he would have only been aged 16 – 17 years old in 1893 – 1894. Perhaps Fleming just kept the old partnership name while being the sole individual partner until his own death prior to 02/3/1893).
1893 – 1894 – Jas Wood, Etna and Atlas Brickworks, Bathville, Armadale Station, Linlithgowshire; office, 28 Royal Exchange Square.
25/03/1893 – Linlithgowshire Gazette – Patrick Duffy, brickmaker, Bathville charged with assaulting Helen Hempseed, brickworker, Armadale by compressing her throat and striking her head against a wall. He was found guilty and fined £2 or 3 weeks imprisonment.
07/12/1894 – Glasgow Herald – Fire brick maker (good) wanted. Constant work to a steady man – Apply Foreman, Atlas Brickworks, Armadale, Bathgate.
21/06/1895 – Glasgow Herald – Moulder wanted for Atlas Fire Brick Works, Armadale. Constant work for a good man. Apply Manager at the works.
Below – 1896 – Atlas Brickworks.
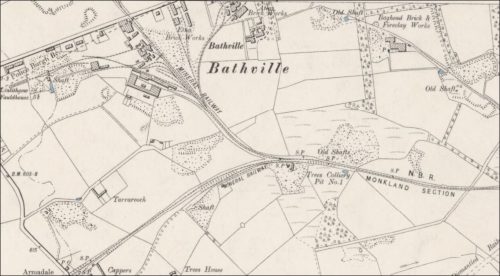
07/11/1896 – Airdrie and Coatbridge Advertiser – Glasgow Royal Infirmary – Contributors include Jas Wood Limited Etna and Atlas Brickworks, Bathville – £3 15s.
14/09/1899 – Glasgow Herald – Brick moulder wanted. Constant work – Apply Foreman Atlas Fire Brick Works, Armadale, Linlithgowshire.
05/10/1900 – Linlithgowshire Gazette – Wanted, a few women and girls at Atlas Brickworks. Good wages and constant work. Apply to the foreman.
Below – 26/10/1900 – Linlithgowshire Gazette – A history of brickworks in the Bathgate, West Lothian area.
One of the most important of our local industries is that of brick making. Quite a number of works, some of them of considerable dimensions, are devoted to this branch of trade, and it would astonish our readers were they told of the vast quantity of bricks which weekly leave this district. That the industry is flourishing in a most remarkable degree is evidenced by the many extensions carried through at most of our local brickworks in recent years and certainly, within the last ten years, the progress made has been enormous. There have been one or two local factors which have lent themselves this increase. There is, for instance, an abundance of clay of a suitable character; then the presence of so many collieries the district makes this a particularly good field for brick making; and not the least of the factors which have contributed to the success of the industry has been the enterprise displayed by the various firms which devote themselves to this class of business. Brick making appliances play so large a part the manufacture of bricks that, in comparison to the large output of material, the number of hands employed is small, yet when we take into account the number and the extent of the brickworks in this neighbourhood, and the very large business which is done, the number of workers, male and female, engaged in this particular branch of trade run into many hundreds. The oldest brickwork in the district is that owned by Messrs Robertson, Love, and Co., it having been in existence for nearly 30 years. Robert Muir and Co. had also an old brickwork before they started their present one. Boghead Brickworks were erected by Mr Gillies of Boghead, and the works were originally used in the manufacture of fire brick and ground fireclay. Years ago the business changed hands, Mr Gillies parting with it to the Boghead Fireclay Company. It was then a small concern, but to meet the growing demands of trade this firm were obliged to considerably enlarge it. They afterwards sold the works to Messrs Dickson and Mann, who a few years later disposed of it to the present proprietors, Messrs Muir and Co. As the demand for the bricks produced in the works continued to grow, a further large addition had to be made, and yet another is in progress. The enterprising firm of Messrs Muir and Co. are, we learn, also making preparations for turning out at these works composition bricks, in addition to those classes bricks presently produced. The works at Bathville owned by James Wood and Co., are of vast dimensions and are divided into two portions, the Atlas and the Etna Brickworks. The Atlas Works are entirely devoted to the manufacture of firebricks, while at the Etna Works composition bricks are produced. An idea will be had of the extent of these works when it is stated that they cover nearly twenty acres of land. In the Etna Works, some 100 hands are employed, while at the Atlas Works there are about 50 workers. At both works, the firm could employ many more hands, but at present, when the trade is so busy, brick workers are not to be got. The Atlas Brickwork is the older of the two. It was begun in a small way a good many years ago by Mr Robert Fleming of Coatbridge, who had as a partner Mr Kopel Moritz. The latter subsequently dropped out of the partnership and removed to the Armadale Brickworks. He continued to be associated with those works till his death, after which the works wore acquired by Mr W. D Samuel and Mr Robert Muir, the present managing directors and original partners of Robert Muir and Co., Ltd., who own Armadale, Barbauchlaw and Boghead Brickworks, and whose fireclay and firebrick products are exported in large quantities to Singapore, Rangoon, Durban, Delagoa Bay, etc. Mr Fleming carried on the Atlas Works himself for some years after the dissolution of his partnership and on his death, the business was acquired from his trustees by Mr Wood of Bathville. Mr Wood threw into the concern considerable enterprise and business ability. He considerably developed the trade and not only made extensive enlargements at the Atlas Works but on his adjoining ground, he erected the Etna Works. Both works are fitted with the latest machinery and improved appliances for the manufacture of all kinds of bricks, and a very large and rapidly growing business is done by the firm. James Wood, Ltd., have their two works fully employed, so far as labour is to be had, in the production bricks alike for the home and export trade. It would be divulging what the firm might regard as a trade secret were we to state the average weight of the bricks which weekly leave their works. It is enough to say that weekly production is enormous and that it is continually increasing. The firm’s products find their way into almost all parts of the world. The firm have good agencies and a splendid connection abroad, and firebricks and ground fireclay are largely exported to Bombay, Calcutta, and elsewhere. As illustrating the advancement made in the method of brick making, it may be mentioned that the kilns now used for the manufacture of composition bricks are those of the continuous Hoffman principle, whereby immense heat is transferred from one chamber to another, and an immense saving of coal is ensured. In the older brickworks in tho district, the Newcastle kilns are still in operation for making firebricks. With these kilns, makers have to make their bricks and dry them in a shed with whatever heat they can get. If steam is employed, it is let underneath the kilns by flues, and the heated air dries the bricks. Under the new Hoffman kiln system, however, the bricks are simply taken from the machine and put into the kilns and the hot air follows gradually around. After the brick chamber is emptied it is immediately filled with fresh or green bricks and the heated air from the burning chambers is conducted round in flues underneath the floor of the kilns. By the new method, the bricks are of course quicker and better made. The fireclay comes from the pits in ‘trips’ and the workmen empty it on to a travelling table and hence into a grinding mill. The clay is then lifted from the pit under the grinding mill by elevators up to the sifting loft. Then it goes through sieves, travels down a shoot to the mixer, where there is a constant stream of water flowing and where by means of knives attached to the machine the clay is mixed and pressed into the brick making machine. The clay comes from this machine as a perfect brick. Thereafter the bricks are placed in the Hoffman kiln and in 14 days time they have taken the form of the first-class commercial article ready for market. It will be seen what a revolution this improved method of brick making must have wrought in the brick making trade when it is mentioned that under the old system in good weather, 14 days were required to dry the hand made brick, while 14 more days were occupied in the burning of it. At present an addition consisting of a large drying shed of considerable dimensions is being made to the Etna Works and this addition, when completed, will permit of a greater output of material and lead to the employment of additional hands. The works are managed by Mr Findlay who succeeded the late manager, Mr Hugh Dunlop, who had been connected with the works from the start and who died a few months ago. We can only mention the other brickworks in the district. That belonging to Robertson Love and Co is prospering like others. Mr John Nimmo and Sons have done a fair business at their works while the Armadale Coal Company have kilns in the course of construction for a large new brickwork. The possibilities of the brick making trade of our district are very great. Situated as Bathgate is almost equidistant between our 2 great commercial cities, Edinburgh and Glasgow, and on the mainline of the railway, there is every certainty that this industry has a bright future. Its growth has been rapid but it is only still in its infancy. When the present factors which are tending to so greatly to depress the building trade have been removed and when the money market is such that it will permit the speculative builder to build as before, the trade will come away with an almost unprecedented boom and much of the new business will naturally come to this district. It is therefore not to be wondered at that some firms are, in anticipation of this demand, enlarging their works and further additions may be anticipated. From a calculation made by a gentleman immediately associated with the trade, some 120,000 composition bricks leave the brickworks in this district daily.
22/01/1902 – The Scotsman (I am uncertain which Armadale Brickworks this article refers to but I have included it here so that it does not go unmissed!) – For sale belonging to the executry estate of the late Mr Marshall, contractor. Portable engine at no 9 pit, Armadale, bricks large quantity, Fireclay pipes large quantity and various sizes, whinstone sets and couplings, freestone jambs, pan mill at new brickwork, Armadale. Bricks (40,000 already cleaned at No 8 Pit, freestone large quantity not including iron. The articles will be shown to enquirers Mr David Sclater, Clerk of Works, Uphall.
Below – 21/03/1902 – Linlithgowshire Gazette – An article discusses the Boghead, Bathville, South Broadrigg, Etna and Atlas Brickworks of West Lothian.
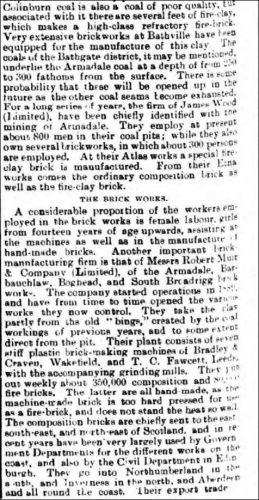
.
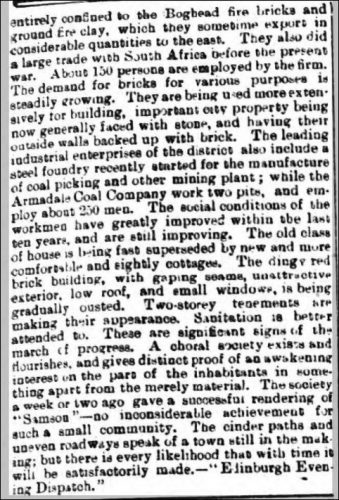
11/06/1902 – Kirkintilloch Herald – Proposed Scottish coal combine – So far as evidence goes (writes a mining correspondent) the rumour of a Scottish coal combination is not without foundation. Representatives interested in such a trust are systematically visiting, for valuation purposes, the collieries of those firms who might be disposed to consider the formation of such an amalgamation. Combine visited the collieries of Messrs Jas. Wood, Ltd., in Armadale district. The pits owned by this firm in Armadale district, of which a valuation was taken, together with the siding accommodation belonging to the firm, are as follows;—No. 2 and No. 7 Northrigg, Nos. 2, 5, and 8 Polkemmot, and No. 4 Hartrigg and Colinshiels Pit, while they own Drumpellier Pit, Coatbridge; Meiklehill, Kirkintilloch: and Neilston, Kilsyth. The firm also owns Atlas and Etna Brickworks, which have a large output.
01/07/1902 – Dundee Evening Telegraph – The Scottish Coal Combine – Today the various collieries and brickworks belonging to Messrs James Wood Limited and the collieries belonging to the Armadale Coal Company will be formally handed over to the syndicate known as the Scottish Coal Combination. Yesterday representatives from the Glasgow office of the combination for stock-taking purposes made a survey of the whole material on hand, furnishings and coal etc, exclusive of the working colliery plant at the different collieries, along with the coal foremen. Messrs James Wood Limited own the following collieries in Armadale district: No 2, No 8, No 6 pits, Polkemmet, No 4 Hartrigg, Nos 2 and 7 Northrigg and Colinshills and also the well known Atlas and Etna Brickworks. They further own Drumpelier Colliery, Coatbridge, Meiklehill, Kirkintilloch, and Neilston Colliery Kilsyth. They employ over a thousand men in Armadale district. The Armadale Coal Company own the 2 pits Nos 17 and 23 Buttness.
02/05/1905 – Edinburgh Evening News – Labourers wanted – Apply Topping, Atlas Brickworks, Armadale.
Below- 19/06/1908 – Linlithgowshire Gazette – United Collieries Limited per the Atlas Brickworks, Armadale sued in court for damages after a 16-year-old youth was scalded.
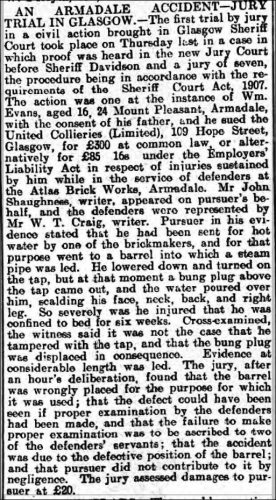
17/07/1908 – Linlithgowshire Gazette – The holidays started at Dickson and Manns works on Wednesday, and will continue till Tuesday, 28th. The Etna Brickworks are only to be closed for four days, but the Atlas is to have three weeks, and the collieries will be closed from the 16th to the 27th.
27/08/1909 – Linlithgowshire Gazette – Brickworkers excursion. The employees of the Etna and Atlas Brickworks, to be in line width the other works of the district, organised an excursion to Portobello, which took place on Saturday by special trains. The excursion was not so well-patronised by workpeople as was expected, although the works were idle for the day to allow them the privilege, but those that did take part in it spent a very day enjoyable visiting the Marine Gardens, and breathing in the salt sea air, and returned at night full of the spirit of enjoyment.
12/09/1909 – Linlithgowshire Gazette – Etna and Atlas Brickworks export to Canada … there is a large order for a million bricks that is being shipped from Etna and Atlas brickworks to Canada that is taking up all the extra wagons. When this order has been discharged more waggons will be had for coal …
Below – 21/10/1910 – Linlithgowshire Gazette – Death of Duncan Richmond former manager of the Atlas and Etna Brickworks, Bathville. He started work at the sites around 1885.
Below – 25/08/1911 – Linlithgowshire Gazette – Drought causes local firms to unite in order to construct a pipeline to bring in water – United Collieries, Etna and Atlas Brickworks, Robertson and Loves Pipe and Can Works. Robert Muir and Co’s works at Boghead Brickworks will be disadvantaged as they will not be connected to this new supply but their Armadale Barbauchlaw Works may be able to secure a supply of water from their own resources.
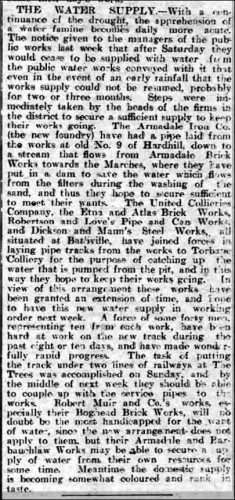
06/02/1914 – West Lothian Courier – Jeannie McComisky, brickworker, Bathgate was charged with having on the 28th January at the Atlas Brickworks, Bathville, occupied by the United Collieries Limited, assaulted Mary Brown, brickworker, Armadale by beating her with a brick mould and seizing violent hold of her by the hair of the head and conducting herself in a disorderly manner. The girl said she got the ‘sack’ on Wednesday. The Fiscal said his information was that this girl had picked a quarrel with the other girl, threw the mould at the girl, knocked her down, and gave her a considersible amount of beating. She then went away but came back and threatened to give her a good deal more when she got an opportunity. The accused said the girl Brown had a spite at her and had been nagging at her for a long time. At the same time, it was not the case that she attacked her with a brick mould and neither did she throw it at at her but she did strike her. The Sheriff – My advice to you is to drop this matter out of your thoughts. Think no more about. You have got ‘the sack’ as you say and that will be sufficient punishment. You may go.
07/05/1915 – Dundee Courier – Wanted – 2 fire brick moulders, steady work, good wages, every encouragement given to suitable men. Apply Manager, Atlas Brickworks, Armadale, West Lothian.
08/05/1915 – Dundee Courier – Panmillman wanted for wet pans; steady work, good wages; every encouragement given to a suitable man. Apply manager, Atlas Brickworks, Armadale, West Lothian.
17/03/1916 – West Lothian Courier – Tribunals – Bathgate … The United Collieries, Ltd. appealed for three workers—James Mclntosh, Lower Bathville, Atlas Brickworks; James Stewart, Meadowhead, Bathgate, kiln burner and Samuel Evans, fireman and engine driver. McIntosh was granted a conditional exemption, Stewart was exempted for three months, and Evans exempted for one month. Mr Leckie, Glasgow, who appeared for the Company, said that of 100 men serving before the war 20 had joined the colours. They were having great difficulty in getting Government orders executed.
21/03/1916 – Daily Record – Men wanted immediately for temporary employment during this week discharging magnesite from wagons on to the ground; 6d per ton will be paid each man as soon as wagons are emptied … The Eglinton Silica Brick Co Ltd., Atlas Brickworks, Armadale.
23/06/1920 – Coatbridge Express – History of Dundyvan Brickworks. The employees of the Eglington Silica Brick Company Limited at Dundyvan Brickworks had their annual trip to Lanark on 5th June and a goodly company enjoyed the outing in the ancient burgh. Mr Wm. Donald, general manager, was present and at the conclusion of dinner, he made interesting reference to the history of their works.
Many trades, he said, that put out enormous efforts for the country during the war have had to pause and look around now that the war is over but with us it is different. Our trade is to supply the requirements of the steel trade and if the steel trade is busy, we shall be busy. Our duty is to see that the steel trade is never short of supplies of magnesite bricks. Another of our duties is to see that they get plenty of ground magnesite. And, as soon as we can, we should make them some chrome bricks, but we can’t do that while we are busy on magnesite bricks. When we do all we can, we are doing our bit. That is why you are all so busy, and you can understand from what I have said that we could have plenty to do for a long time ahead.
If we do all we can to keep the quality up to our highest level we will always have plenty to do, and something to spare for others in the trade. It doesn’t do to be the only arm in the trade. I find the other members real good friends, we have an Association – The magnesite Brickmakers’ Association – so that in addition to being members of your own Societies you are members of the Magnesite Brickmakers’ Society. Some of you will know, and others I think will be interested to know, that in 1871 there was another war in Europe. At that time it was Germany and France who were fighting over Alsace and Lorraine. Some of you know Alsace, where Metz is, opposite and near to Verdun, and others will know Lorraine where Strasbourg is. Germany won and occupied Paris, and France had to pay up. Now the tables have been turned and France has got back the Alsace and Lorraine countries taken from her.
Now, it was soon after and as a result of that Franco-German war that the Eglinton business first began. Land was got at Irvine harbour, and works were started to make chemicals that were in great demand. Limestone wait required, and the best stone was in County Antrim, but they couldn’t get enough, so my father went over to Ireland and out the Glenarm Quarries from Lord Antrim, built a pier, and built two steamers and got his limestone that way. In that limestone there were beds of flints and flints were bad for the chemical works, so that had to be removed from the limestone and soon a good many thousand tons of flints accumulated and had either be made into something or cleared out of the way. Well, as a result of that war steel was required, and the Blochairn and Hallside Steel Works were erected in Scotland and required silica bricks. My father knew that silica bricks were being made from flints on the Thames or were trying to be made, and be decided to make them on the Clyde. At that time Roberts had a foundry in South Wales where he made castings for brick machines like what we used to use. After giving his price for brick machines he offered to supply mills and to build stoves and kilns and the result was that he gave up his business in South Wales and came to Scotland with Norman and Jim Hannaford, who is now the foreman at Braehead. Roberts became the first works manager at Dundyvan, and the stoves and kilns were built by Mr Jamieson, the builder, to the plans that Roberts brought with him from South Wales. So that Dundyvan with all these Welshmen began as a colony of South Wales -a little New South Wales. That was in 1889. There have been ups and downs since then. At first, the steel trade of the Clyde was most affected with the Clyde shipbuilding. When therefore shipbuilding was busy, so was Dundyvan. After Roberts, the manager was Norman, then McGregor, the man with the one arm and then Dan Fraser. Fraser left in 1909 and it was that summer I came among you and became the works manager for six years. You will remember that my father was run over in January 1915. At that time I was far from well and he was Dundyvan every day. One morning he came down early and came in at No. 3 gate. The pugmen didn’t see him, and the pug came round the corner too quickly and my poor father couldn’t get past quick enough. A good many of you will remember my father and his great interest in all stages of manufacture. Sometimes he was too particular. But he was an exceedingly goodhearted master, and to all who knew him well, a good friend. He had a wide circle of friends. His death made it necessary for me to take up the reins, and I wasn’t long in seeing that with the altered circumstances of the war, calcined magnesite couldn’t be got. We would have to take cargoes of raw magnesite. Now the Dundyvan kilns at that time weren’t enough to do much calcining, burning of slap bricks and burning of finished, and 1 made up my mind that, I had to get hold of another Works. At first, I thought of Braehead but I soon saw that wouldn’t do what would be required without more plant first being erected at Dundyvan, so I leased Garnqueen, with the expectation that the kilns there would at least be able to do the calcining. The cost of upkeep of these kilns working at our high temperatures was very great for the work they did and the quality of the calcined magnesite produced was not nearly so good as what can be done at Dundyvan.
Relating the work done during the war Mr Donald said – By October 1916, we had become the largest makers in this country. In October that year, the steel trade wasn’t getting enough. So all the makers were called to the Ministry of Munitions and we were all asked what we could do. I promised to increase our production by a quarter within three months and I was asked to do it When that was done I was told one day that bigger supplies would be required. Could I do anything more! Well, I knew myself from the orders I had to refuse that more was required and I had been making enquiries about other works I could get. So I promised to come back in a week and let them know what could be done. Well,, when I came to Scotland the likeliest works were Shawsrigg Works, Larkhall, and the calcining kilns at Armadale. So I went back in a week. I remember it was 4 o’clock, on a Saturday afternoon, and I offered to double the production within two months if that was wanted, provided I could get more magnesite and provided I got some Garnqueen man back from the Army. That was promised, so I went ahead, the kilns at Shawsrigg were muffle kilns. These muffles had to be cleared out. The old set of kilns had to have their crowns put right. A brick machine had to be got to Shawsrigg and erected there and the mills had to be thoroughly overhauled. The works had been idle for two years and workers had to be got. The railway siding plant had to be extended, and the water supply was bad. A new pump had to be got, and so on. Also, we had to get another machine for Garnqueen so that we could depend on one always being right. We had also to get a second lightning crusher. The first lightning crusher had been got from Braidwood. The first machine came from London. Another was got from Irvine. The next was got from Gloucester. The next was got from Hull. And the next was got from Dublin. It was only by getting them second hand from where they existed, in works that were closed down, that the machinery could be got in time. Well, that gave us Dundyvan, Garnqueen, Shawsrigg and Armadale. At Armadale, all we did was calcining. Calcining was also done at Shawsrigg and Garnqueen, as well as slap bricks, and the first burning came to Dundyvan to be made into finished bricks. Later there wasn’t ever then enough, and we had to take the works at Kilmarnock. There was great excitement at that time. I had already entered into a contract to supply the French Government with three-quarters of a million magnesite bricks. Now Italy had joined the Allies and a representative from their Ministry of Munitions in Rome called at 45 Renfield Street and asked what we could do. I said quite simply that there was no limit to what we could de if we had enough magnesite and enough works to make bricks. So they asked me to supply a quarter of a million, delivering 50,000 in May, June, July, August and September in 1916. As soon as the arrangements were completed I went ahead at Southhook Works near Kilmarnock. One of the ‘Clan’ Line arrived from India. The raw magnesite was sent straight down there. Soon we began to get it into slap bricks and got them out too. So the production game began on a bigger scale. Well, we were up to time with the increased production. A wire came from the Ministry saying they had a wire from Italy wanting the bricks. Where were they? So I replied they were still in the kiln but the kiln door was down the previous day and we could have them packed up and despatched that week. That was how the thing went on and by September 1916 we had delivered the 750,000 to France and the bricks to Italy as well. That having been done the question was – What next? Well, the usual course of business is to execute orders but during the war, more questions than that had to be taken into account. The Germans settled this particular question for us. They sank two steamers with magnesite and made such havoc with their submarines that it was decided to restrict all exports and only to import magnesite to meet the demands of the British works. These were going to be very great, and it would be difficult to get all the supplies of magnesite from Greece that would be required.
It was decided, therefore, that Southhook and Shawsrigg Works and the Armadale Kilns would be given up and we would work away with Dundyvan and Garnqueen. In the meantime Dundyvan had grown. We had kilns 9, 10 and 11, and at Garnqueen we had built eight Newcastle kilns. At Dundyvan also we had added stoves 5 and 6. Since the Armistice we had the sale at Garnqueen of all the spare machinery and since then we have gone ahead at Dundyvan setting our house in order. That is what the steelworks themselves had been doing, and soon their orders came along again. This time with increasing orders. I made up my mind that to get the extra plant to give the increased production I wouldn’t go back to fireclay works, but would erect the most modern plant at Dundyvan, taking the erections decided on in their order of most importance. When we get erected all that has been purchased we shall have the best magnesite works in Great Britain.
There is a good old saying that “All work and no play makes Jack a dull boy”. More than that, however, it makes him less able to concentrate his attention to matters that his competitors pay attention to. All workers in any branch of trade have competitors in that same branch of trade either in the adjoining street, town, county or country, and it is just as necessary for each worker to consider his work in that light as it is for the employers to think how they can compete with other employers by the introduction of better machinery and plant. Employers depend on the machinery and plant being worked with the highest skill, and with the greatest economy. It is up to the workers to back up the employers and each to compete, with the workers who are doing the same job in the towns or in other countries. On the other hand, it is up to the employer to consider whether they can assist the workers by giving good working conditions, light and fresh air, protection from bad weather and warmth whenever necessary. In country districts it is often necessary to provide travelling facilities and housing accommodation. In towns like Coatbridge, where the workers have the choosing of the town councillors just as much and even to a greater extent than the employers have, they can introduce in their towns good education, good lighting, good tramway travelling facilities, good drainage, and in these days of town planning they can also introduce good housing schemes. In works that are situated in burghs or towns, the employer has taxes to bear that lighten the burden of the residential inhabitants and the workers, so that the inhabitants are all the better able to have the best conditions of life in their midst. It is mainly in their works themselves that the employers have their responsibilities, but my opinion is that it would be good for all employers if they gave their workers ground for development in allotments so that their interests in many of the things they have learned in their youth in country districts can be sustained. It is my hope that soon will be able to provide our workers not only with improvements in the working conditions at Dundyvan in many respects but also that at no distant date we shall have a field, part of which can be used as a football field either by the younger workers themselves or by the children of the older workers and in part of which the workers will have allotments that they can cultivate for the growth of vegetables and flowers. You will see from the coloured print of the Veitsch Company’s Works and buildings that they have a bandstand and laid out gardens for their employees. If they had not deployed their works first they would not have gone in for such wonderfully good developments in these directions. But their enterpriser before the war was really wonderful, and their spirit I hope to develop at our works in Coatbridge. The Veitsch Company are far away among the Austrian Alps. A panoramic view of these is exhibited. The works are five or six miles from any railroad and all their bricks and bags of magnesite have to be carted through a narrow valley to the Murs Valley where the lines run either east or west, either to Trieste, which is shown on the map, where shipments take place or towards Vienna where the railway lines distribute the goods to the various consuming centres. Shipments at Trieste are very difficult just now. Steamers take a long time to load. There are very few locomotives in the country. Such as there are, are using wood logs as fuel. You can imagine how much steam we could keep on our main boiler if we had only wood to burn. You can imagine how many carriages could have come from Coatbridge to Lanark today if the engine had logs of wood to burn instead of coal. I met a man recently, the representative of a very large Paris and London firm, who told me his principal was travelling from one end of Austria to the other, and also in Germany and that it was an ordinary occurrence for trains to stop between stations and for any timber near at hand, either fences or gates, or even parts of the carriages them, selves to be collected by the passengers so as to provide enough wood to steam the engine to the next station. My brother law is in that part of the world just now, and he tells me that the trains travel with only one-third of the usual carriages and that even though you have been travelling for two days and two nights in succession and are tired out, you can’t sleep in the trains for the shaking, and the jolting.
While they have plenty of food in the country districts, the food in the cities sells at ransom prices. They have no transport facilities. Coal costs anything from £15 to £20 per ton. You can imagine therefore, with no coal supplies how many kilns they can with logs of timber, and how many tons of dead burned magnesite and magnesite bricks they can supply. Of course, their competition is bound to come later, and it is for that reason that we are doing all that we can overtake to get erected good milling plant and good calcining plant so that we can do at our works all that they can do at theirs. When our plant is erected it will be up to the workers to work the plant with the highest skill. Your will compete with the labour of the Continent to do the work to the highest standard and as economically as possible. Wages will not come down until the cost of living is greatly reduced, but all workers should consider whether they cannot give a little more production. That may only be possible if the machinery or plant is altered so as to suit better the labour being done. The intention with us will be to give any proposal that is put forward by any of the workers in that way every consideration possible. Now, there is no use of speaking in generalities without giving an application to those general ideas, and I would like to refer in a few words to two matters that I know have been very much on the mind of our works manager. One of these has to do with the percentage of rejected magnesite bricks and the other has to do with fuel consumption.
I think the workers are to be congratulated on their having fixed an annual dance as you did last winter and also on the annual trip which you are beginning today. Whoever it was who originated the idea deserves credit. I shouldn’t be surprised if it was Maggie Toal and if it was, her name should be remembered and go down to posterity in the history of the works. I am more glad still that you are having such a fine day. I think the committee acted wisely in having a set dinner and afternoon tea, as they have done, and also in deciding that for this year they would have drives rather than sports. Perhaps for next year, now that the minds of the workers have become accustomed to the idea of an annual trip they will set themselves to begin to lay up for six months ahead of the trip, and if so they will be able to go further afield, either by train or by motor transport. There is nothing like providing well beforehand, and perhaps you will let me provide you with an idea about next year’s trip. That is, that it should be a trip either to the head of Loch Lomond or to Dunoon so that you could have a complete change of air and a good dose of sea breezes. I think you have been fortunate in choosing Lanark this year so that you can all get to know the county town of our county of Lanarkshire and to know the Falls of Clyde in the neighbourhood. This is one of the oldest burghs in Scotland. It was a place of residence of the Scottish kings before the English invasion of the times of Wallace and Bruce. Some of you may have been at Stirling and know the William monument. You can also see a statue of Wallace before the church steeple in the square. Wallace was one of the greatest men of Scottish history and though he wasn’t born here (he was born at Elderslie near Paisley) his young wife, Marion Bradfoote came from Lanark and it was at Lanark he first became prominent and famous. That’s a long time ago, seven hundred years ago and more, but it is undoubtedly due to his tremendous energy that the Scottish people retained their self-esteem and strength of character during a series of most trying experiences – The Scots came out well. I think it is a somewhat similar experience on much vaster lines that the whole people of this country of ours are emerging from. The recent war was a tremendous experience for all of us while it lasted. But I believe that we have all gained in strength of character and the best way to show that is in the work that we each of us do. Mr Lawson Scott, works manager thanked Mr Donald for his presence and interesting statement.
03/06/1921 – Linlithgowshire Gazette – Public works coming to a complete stand – Week after week one public work after another is compelled to shut down for want of fuel. First the Atlas Steel Foundry had to close down, then Messrs R. Muir and Co,’s brickworks, and next Messrs Robertson and Love’s fireclay pipe and can works, and lastly Messrs Dickson and Mann, Ltd., have had to close their steel foundry, and the Etna and Atlas brickworks, which were well stocked, to begin with, have now also had to shut down for want of coal. Messrs Dickson and Mann could probably have held out little longer as far as fuel is concerned, but the opportunity is being taken to make some desirable repairs on the furnace. They are still carrying on their engineering shops, and the United Collieries are able to carry on their machine shops and wagon building shops, being little fuel required with them. All the chimney stacks being now smokeless, the air is pure that one can’t help commenting what a blessing it would be to humanity if the air pollution by smoke could be entirely eliminated. It’s a poor misfortune that does not yield some compensation.
08/07/1921 – Linlithgowshire Gazette – Brickworks re-opening. With the resumption of the miners on Monday, Messrs Muir’s Armadale Brickwork were set in operation again, the first day’s coal being utilised for that purpose. Other works would start immediately but for the fact that the holiday season is on, and if the workers are asked to work during the holiday week they will be able to demand double pay. The Etna and Atlas Brickworks are not to lose much time before they are turning out their full complement of building brick, and the fireclay pipe and chimney can works are in operation again, the demand for their output being enormous. The foundries don’t seem to be in a hurry to get started. At the Atlas Foundry, some dressers have been working lately clearing away some order, and now, in view of the holidays, notice has been posted that the works will close down on Thursday the 7th till Tuesday the 19th.
02/10/1925 – West Lothian Courier – A friend of Andrew Carnegie. On Wednesday afternoon the funeral of Mr Robert King. Craigpark took place at Torphichen Church Yard … Mr King, who died on Friday last, had reached a ripe old age. In his earlier years, he was well-known in the Armada!e district, where he resided at Woodlands and was the manager in the Bathville Brickworks. About twenty years ago he took up his residence in Torphichen where he has since remained … Mr King and his brothers enjoyed in a peculiar degree the friendship of the Late Mr Andrew Carnegie and his wife, with whom they were on intimate terms. A brother and a brother’s widow it may be remembered benefited considerably under Sir Carnegie’s will. Returning home, some forty-odd years ago, Mr King married, his brother-in-law being Mr James Wood of Wallbouse, with some of whose many activities he was associated during the rest of his life, acting latterly as manager of the Atlas Brick and Tile Works at Springburn in Glasgow from which position he retired some six years … (Note – SBH – I am uncertain as to the relationship between the Atlas Brickworks and Springburn, Glasgow).
Below – 1929 – Etna and Atlas Brickworks from the air.
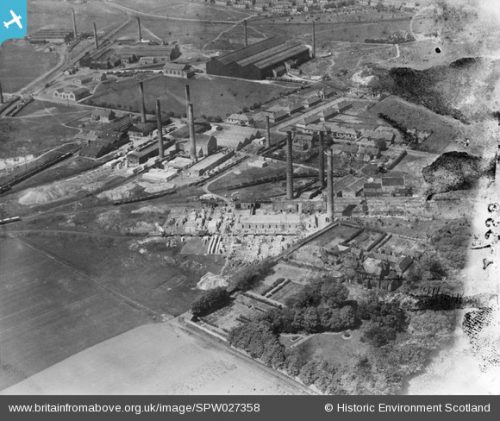
02/12/1931 – Falkirk Herald – West Lothian Industries – Promising Revival in Brickmaking and Hosiery. A promising revival in certain industries in West Lothian is reported notably to the manufacture of bricks and hosiery. One of the busiest places in the country at the moment is the Etna Brick Works, at Armadale, belonging to the United Collieries Ltd. An official stated that there had been a sudden revival of trade, and they were supplying the demand as it occurred. A few weeks ago the daily output of bricks from the works was 25,000, and last week the figure was almost 55,000. Not only has the spurt to the industry been responsible for the employment of additional men, but it has also been found necessary to put on a night shift. A large number of the bricks have been sent to Glasgow for housing achievement. This output of bricks is regarded as really high for a brickwork in the provisional housing schemes in progress in West Lothian are being supplied. The prospect of the brick trade is promising. At the company’s other brickworks at Bathville, the employees are also busy.
Another brickworks at Barbauchlaw, Armadale, belonging to Robert Muir & Co (1930). Ltd., have also doubled their output and business has been much better during the past five weeks. They chiefly export bricks to Canada, South Africa, and India. The employees are working extra time, and the output has been greatly facilitated by the installation of a new plant. There has been a large demand for bricks from the East of Scotland. These works are associated with a concern in Fife, which is also working for steam ahead.
The prospects in the hosiery trades are higher than ever. Mr James Livingstone, the chairman of the West Lothian Hosiery Factory, Ltd., stated that fancy hosiery manufacturing was very busy, and if the manufacturers of this particular brand of hose were successful in their efforts for the tariff the result would be advantageous and the factories in the county would be going full steam ahead. He stated that although Bathgate and Bo’ness hosieries orders were being executed for German clients, and there was plenty of work in hand for the next three or four months. Within a recent week, the boom had been so satisfactory that 120 extra hands had been taken on at Bathgate and 40 at Bo’ness.
So long as the staple industries such as shipbuilding, engineering and electrical manufacturing are suffering from depression, the steel and iron foundries in West Lothian will be affected. According to Mr James Watt, of the Atlas Steel, Armadale, it was very difficult to make a prediction regarding the future of the industry in the County. About a month ago there was a spurt in business, but at the end of last week a lull occurred, but it was coming away this week. It was much better at the moment than it had been, and all that was required was a new confidence. The iron trade, he said, had been badly hit. On enquiry at the works of Messrs George Wolfe & Sons, Ltd., shovel manufacturers it was reported that there had been an improvement in business since the General Election. Their chief manufactures were shovels and rolled steel. They have six employees, and the policy of the firm has been to keep the works going full time.
27/10/1933 – Midlothian Advertiser – Armadale trade improving. A distinctly hopeful tone pervades the district with regard to the lesser industries. At Armadale for instance, there is a boom in brick-making. United Collieries, Ltd., own the works which manufacture the well-known “Etna” bricks house-building, and, the equally well-known brand “Atlas” bricks for the building furnaces and retorts. Both brands are made from clay found locally and are known as equal to any other quality in the trade. With the anticipated development of the blast furnaces in the west; it is fully expected that “Atlas” bricks will be in increasing demand and that greater prosperity is ensured for this local industry.
29/10/1937 – Linlithgowshire Gazette – Fatal accident enquiry. Robert Wood Apprentice Electric linesman, 21 Park Terrace, Armadale was electrocuted on 11/09/1937 at the Atlas Brickworks owned by United Collieries Ltd. After the hearing, a formal verdict was returned.
11/02/1938 – Linlithgowshire Gazette – United Collieries Ltd, Bathville Brickworks, Armadale (See entry above – was it Bathville or Atlas!) were charged with negligence after the electrocution of Robert Wood. After the hearing, the firm were found not guilty.
Below –
1938 – Atlas Fire Brick Works.
1947 – United Fireclay Products Limited comprised of the Etna and Atlas Firebrick Works, The Bathville Pipe Works, the UNICOL Tile Works, all at Armadale and the Brownhill building brickworks at Clelland, Lanarkshire. Lower demand for refractories led to the Etna Works being converted to making building bricks under the ETNA brand and the closure of the Atlas Works in 1973.
22/05/1953 – West Lothian Courier – The death occurred at his home at Station Road, Armadale, last Saturday, of one of the best known and oldest residents in the Burgh. He was Mr John Richmond, aged 92, former manager of Atlas and Etna Brickworks. Armadale. Mr Richmond, who was a native of Braeside, Ballieston, had resided in Armadale for more than 60 years. An expert at his job, he was well-known in the trade throughout Scotland and enjoyed the confidence of employers and employees alike. During his period as manager, he was in no small measure responsible for the high prestige established by Atlas and Etna products in the building trade. He retired many years ago but continued to enjoy good health and remained active until two months before his death. Predeceased by his wife a number of years ago, Mr Richmond is survived by his family of three daughters and two sons. One of the sons, Mr John Richmond, succeeded his father as manager at Atas and Etna Brickworks.
1961 – 1962 – Directory of British Clay Products and Manufacturers – United Fireclay Products Ltd, Head Office 140 West George Street, Glasgow C2. Tel Douglas 8707. Works – Atlas Works, Armadale, West Lothian – fire bricks. Etna Works, Armadale, West Lothian.- fire bricks and building bricks. West Works – Armadale, West Lothian – fire bricks. Bathville Pipeworks, Armadale, West Lothian – drainage goods. Brownhill Brickworks, Clelland, Lanarkshire – building bricks. Trade names – Atlas +A, Atlas and Etna – fire bricks. Etna and Brownhill building bricks.
06/07/1962 – West Lothian Courier – Factory Act Offence. At Linlithgow Sheriff Court on Wednesday, Andrew Taggart Wright, assistant brickwork manager, 4 Marches Drive, Armadale, was fined £20 when he pleaded guilty through an agent to having on 22nd November 1961, at Atlas Brickworks, Bathville, failed to maintain constantly and keep in position fencing for a dangerous part of machinery.
Below – 07/1964 – The Refractories Journal – Product list.
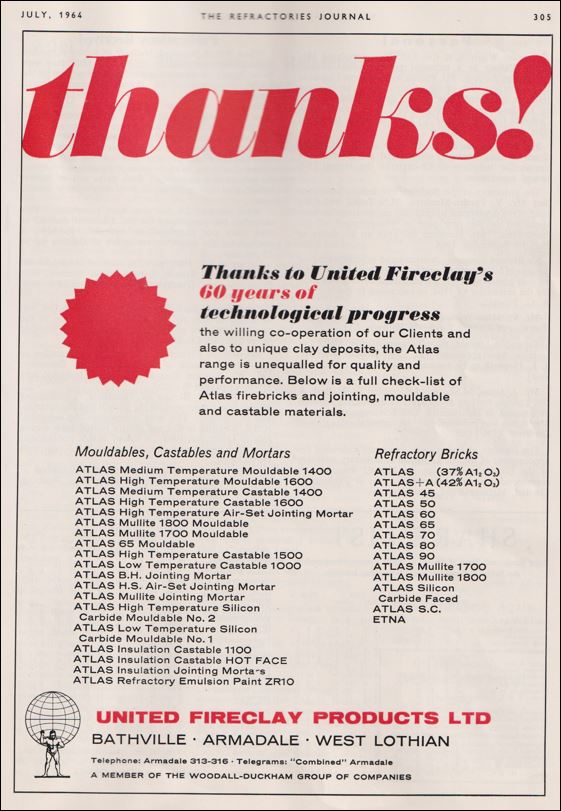
14/08/1970 – West Lothian Courier – Armadale Pipeworks to close down but the effect is cushioned. The closure of Bathville Pipe Works on August 31 could mean as many as 20 people becoming redundant. The company, United Fireclay Products Ltd., are making every effort to accommodate elsewhere the 48 workers who will lose their jobs as a result of the closure and it seems certain that the figure of 20 left jobless will not be exceeded if in fact it is reached. The company as a whole employs almost 400 people so that the redundancy figure is looked upon by the company as minimal. This was said by Mr James Smith, managing director of United Fireclay Products Ltd. who added that the decision to close the Pipe Works was taken only after a review of future market prospects in relation to the overall capacity for pipe production in the United Kingdom. Announcing the intended closure, Mr Smith emphasised. “The fact that Bathville Pipe Works is closing down does not mean that the whole company is dosing down. Indeed, United Fireclay Products. Ltd., incorporating as it does the Atlas and West Fire refractories and fire clay works and the Etna and Brown Hill building brickworks is thriving, with a big expansion programme planned which could mean even more jobs gained than those lost by the present closure. Atlas, for example, is a factory for the high-temperature industries. We supply the big steelworks in this country and we have a substantial export trade to Europe, particularly Holland. Atlas make not only fire bricks from clay from local mines but also refractories from imported materials. People associate the name of Bathville with all our efforts and when they hear the Bathville Pipe Works is closing they may well feel that that means the end of everything. They forget that the Pipe Works is only part of a complex. The managing director added that he had seen personally all concerned putting them in the picture and assuring those not affected by the closure that they had no need to worry about the future. This was followed up with a personal letter to each employee. Although the news is not as bad as it appeared at first, there will nevertheless be a feeling of real sorrow in Armadale that Bathgate Pipe Works, for so many years a feature of life in the town, will be no more.
1973 – The 1985 publication ‘A survey of Scottish brickmarks’ suggests the works closed in 1973. This date is also detailed in an article entitled ‘A look at the Armadale Works of United Fireclay Products’ which appeared c. 11/1978 in the Refractories Journal.
<1978 – An article entitled ‘A look at the Armadale Works of United Fireclay Products’ which appeared c. 11/1978 in the Refractories Journal states ‘The ‘Etna’ brand has disappeared by the ‘Atlas’ brand continues to be used all over the world. (Note – SBH – If the Atlas Works closed in 1973 but the ‘Atlas’ brand was still being exported all over the world then United Fireclay Products were still using the ‘Atlas’ brand name and manufacturing them on site, possibly at the West Works).
Below – The Scottish Industrial Archaeology Survey published a report in 1985 entitled ” A survey of Scottish brickmarks. During the compilation of this report in which the survey officers visited working and derelict brickworks sites, many items of interest were donated or found. Many of these items were thereafter donated to the National Museum Scotland. The item below is one of these items. A brass stamping plate marked ‘Atlas 60’

Below – The Scottish Industrial Archaeology Survey published a report in 1985 entitled ” A survey of Scottish brickmarks. During the compilation of this report in which the survey officers visited working and derelict brickworks sites, many items of interest were donated or found. Many of these items were thereafter donated to the National Museum Scotland. The item below is one of these items. A bundle of stencils used to mark the destinations on wooden shipping crates eg, Quebec, Trinidad, Shanghai, Montevideo. There is also a ‘Made in Scotland’ stencil. Found at the Atlas Works.
.
.
.