Blackpots Tileworks, Whitehills, Banff.
Canmore
Images
These small brick and tile works are situated immediately above the shoreline on the side of Knock Head, Whitehills, about 2 miles W of Banff. The clay used for the manufacture of field drainage tiles is quarried from the sides of a shallow pit in the headland and is transported a short distance on a single-track, narrow-gauge railway to the works where it is processed. The clay tiles are dried by natural methods in a long, single-storeyed drying-shed, and are fired in a rectangular kiln of updraught type contained within a walled enclosure on the NE side. The complex is bounded on the E by an L-shaped farm steading and two domestic buildings, one of which now serves as the works manager’s office. To the NW there is a small harbour with a rubble-built pier.
Some time towards the end of the 18th century one Dr Saunders, who is known to have been in possession of the farm of Blackpots in 1766, established a brick and tile works on his farm about two miles from Banff (SRO RHP 11842). It employed eight or nine men, and had the command of a small harbour for the importation of coals, and exporting part of the manufacture (OSA 1791-9).
The ‘Blackpots Brickwork’ is shown on a small-scale produce plan of 1829, in which the layout of the works appears to consist of three distinct buildings: a long-range which seems to correspond in outline with the overall layout of the existing farm steading, manager’s office and walled enclosure of the kiln; two short parallel ranges aligned NE-SW on the W side of this range possibly represent original drying-sheds (SRO RHP 8840).
In about 1840 the works which employed eleven men during the summer season was beginning to manufacture drainage tiles in addition to roofing tiles (NSA 1845; SRO Seafield Muniments, Tenants Ledger for Banff, Whitehills and Ord, 1842-50), and probably assumed its existing layout at about this period (Scot Stud 1971).
The production of pantiles was discontinued at the beginning of this century (20th), and perforated wire-cut bricks were last manufactured in about 1946 (Information from works manager), by a series of dampers in the roof of the kiln.
There are three square, brick-built chimney-stacks, two at the Wend, and one at the E end, the base of which is constructed in whinstone rubble masonry. The existing kiln was rebuilt as recently as 1953 but appears to represent a modified form of the traditional updraught type.
Architectural description:
(a) The principal feature of architectural interest is the drying-shed (Rasmusson and Meyer 1968), which is of modular construction but has a pleasing irregular external appearance, particularly in its subsided wavy roof-line. The building is rectangular in plan, aligned almost due N and S on its long axis and measuring 234 feet in length by 28 feet 6 inches in width, with a machine-shed wing projecting from the centre of the W wall forming a T-shaped layout overall. It is a single-storeyed structure, covered with a double pitched pantiled roof, with hipped ends on the drying-shed. The machine shed roof is gabled at the W side, and the gable wall is constructed entirely of rubble masonry.
The roof structure of the drying-shed is carried on a timber wall-plate supported at the angles of the building and about mid-way along the side walls by stone piers. The piers, which have a slight external batter, are constructed of whinstone rubble masonry. The wall-plate consists of scarf-jointed sections, half-lap jointed at the angles above the stone piers. Intermediate point supports are provided by a series of timber posts spaced at 8 feet centres. The posts, which are notched to receive external raking struts, are set on rough stone bases and are nailed to the soffit of the wall-Plate. (a similar form of construction concealed beneath horizontal weather-boarding was noted in the former drying-shed at Anniston Brickworks, Inverkeilor, Angus, demolished 1971). For the purposes of ventilation, each bay between the posts on the side walls contains an upper and lower hopper-hung louvre, locally known as a ‘pass’. The wooden louvres are composed of close-jointed boards, ledged at the top and bottom, and are pivoted on strap-hinges having drawn ends of circular section directly penetrating the timber posts. Tar is applied periodically to the posts and louvres for the purpose of preservation and forms a distinct contrast of colour with the red pantiled roof. The louvres are secured in an open position by roughly-hewn props. There are three entrances in the sidewalls, the principal opening in the centre of the E wall, almost directly opposite the kiln, being protected by a wooden V-section rhone housed in a notched timber bracket. The end walls of the shed contain three twin-leaf doorways with crook-and-band hinges, and the bays between the doors are protected by vertical or horizontal weather-boarding strengthened at the N end by raking struts which represent re-used boat ribs.
Internally, the drying-shed is laid out on a three-aisled plan with four parallel rows of drying-racks and two transverse passages opposite the entrances in the side walls. The floor of the shed is composed of earth with an admixture of ash taken from the kiln. The drying-racks average about 6 feet 6 inches in height and 8 feet 3 inches in length. The board length is governed by its load-bearing capacity of ‘green’ clay bricks and tiles and determines the bay module (Rasmusson and Meyer 1968). The racks are of simple wooden box-framed construction with four angle-posts and closely-spaced shelves originally reinforced by iron ties bolted into the corner-posts. In the original arrangement, the two middle rows of drying-racks appear to have been double-banked sharing a common set of central posts.
The roof structure of the shed consists of collar-rafter couples with the members normally of half-tree section. The pantiles of conventional ‘S’ section overhang slightly at the eaves and are hung loosely by the usual nib-head on timber cross-battens laid on the common rafters. The ridge and hip tiles are of segmental section.
(b) The brick-built kiln is rectangular in plan measuring 39 feet 9 inches in length by 16 feet in width. It is completely
roofed, and the covered stoking-aisles contain staggered rows of furnace-holes in each side of the kiln beneath the level of the kiln chamber. During the firing process, a segmental arch-headed doorway in the W wall of the kiln is thermally sealed with old bricks and an external coating of clay and sand. The chamber itself is covered with a segmental-arched barrel vault built of special-made bricks and measures 10 feet 4 inches in height from the floor to the crown of the vault.
The floor of the kiln, which measures 32 ft by 12 ft internally, consists of 12-inch bricks laid on edge in a honeycomb fashion above the furnaces. During firing, the temperature of the chamber is controlled by a series of dampers in the roof of the kiln. There are three square, brick-built chimney-stacks, two at the W end, and one at the E end, the base of which is constructed in whinstone rubble masonry. The existing kiln was rebuilt as recently as 1953 but appears to represent a modified form of traditional updraught type ( a ruinous double-banked kiln, charged from furnace-holes in the side walls beneath the floors of the kiln chambers, was noted at the former Tochieneal Brickworks, Lintmill, near Cullen, Banffshire. Each kiln chamber was rectangular on plan and roofed internally with a segmental-arched barrel-vault. Two wood-fired brick kilns on Ashburnham Place Estate, Sussex, were of the updraught type, and were open at the top; old bricks and sand were used to roof and seal the kilns when they were charged. The kilns ceased operation in 1968 (Gordon, Country Life, July 1969). The older types of Danish blast-furnace are also fired from beneath the kiln floor, and are either open at the top, or covered with a tiled floor [Rasmusson and Mewyer 1968]).
Manufacturing process:
In each alternate week during the season from April to October blue gault clay is quarried manually, and is dampened with water to the correct consistency at the quarry face. It is transported a short distance to the works on a single-track railway in four-wheeled wooden bogies with flat-rimmed iron wheels; the bogies are hand-operated and controlled by a simple wooden brake lever. The railway is of 2 feet 9 inches gauge and is composed mainly of L-section steel rails with the flange turned outwards. From a turntable in the centre of the clay pit, the railway is 414 feet in length down a gradual slope to the works, where it is supported on a bridge near the apex of the machine-shed gable wall. The clay is gravity fed into a vertical pug-mill, which churns the watered clay, forcing it downwards through an outlet at the base.
A plunger or ‘grater’ with two pistons removes the stones, which occur mainly in the surface deposits, and the clay is then mixed in a horizontal pug-mill or auger with a screw drive. A twin-piston extruder or pipe-machine, also known locally as a ‘silly’, forces the clay through two pipe dies, and the moulded sections are cut into suitable lengths by a hand-operated wire-cutting machine. A wire brick-cutting machine, formerly used for perforated bricks, is now stored in the nearby steading. The clay is lifted by hand between each of these mechanical processes, all of which are powered through shaft-drives and gearing from a single-cylinder 36 h.p. Shanks diesel engine housed in a rebuilt shed on the N side. An original steam engine used for this purpose was subsequently replaced by an oil-fired engine, and the existing machine was installed in about 1927. The ‘green’ clay tiles are carried in three-tier tile barrows, or ‘horses’, to the racks of the drying-shed, where they are dried in a slow, natural process for about three weeks depending on climatic conditions. Once dried, the tiles are transported on single-tier ‘barrows’ to the kiln which has a total capacity of about 40 tons of ware, that is, 14-15,000 pipes. During a summer season, the kiln is normally fired on sixteen separate occasions. A single firing lasts for about 40-45 hours, consumes eleven tons of coal, and the kiln chamber usually reaches a maximum temperature of about 1000 degrees C. The tiles are graded as ‘firsts’ or ‘seconds’ according to quality.
In one season the works have a total average output of 1,200 tons of fired clay with approximately one-third wastage rate.
There are estimated reserves of more than 1 million tons of clay on the E side of the Knock Headland (information from the works manager, citing a report by J W H Ross and Company, Glasgow, 27th June 1969).
Visited by RCAHMS (GDH, GS), 28 May 1971
(Location cited as NJ 661 658). Blackpots Brick and Tile Works. Late 18th century. A most interesting complex consisting of a single-storey rubble and wood building, pantiled, roofed, on a T-plan, a brick-and-rubble kiln, a 1-storey dwelling house, and a cart shed and stable block. The downstroke of the T was the moulding shop and the cross-stroke was the drying-shed. The core of the kiln is rubble, as is the base of the chimney. The lean-to additions protecting the fire-holes and the top of the chimney are of brick. A primitive plateway linked the works with the claypit in the cliff behind. Disused, and falling into decay.
J R Hume 1977.
(Also known as Whitehills). This works had one kiln (of rectangular updraught type) and were in use from about 1786 to 1971; it had been demolished by 1979.
G Douglas and M Oglethorpe 1993.
1766 – Dr Saunders owns Blackpots Farm and at some point after 1766 he erects a brick and tile works.
26/02/1781 – All those who are indebted to Doctor Robert Saunders, late in Banff for brick and tyle or any other manner or way whatever are required to pay in the same to Alexander Dockar, writer in Banff on or before the twentieth day of March next otherwise prosecutions will be raised against the outstanders. Not to be repeated.
10/03/1800 – Aberdeen Press and Journal – Brickfields near Banff – The great rise of labour, the high price of coals, and the difficulty of obtaining them, expense of carriage, &c. Mr Saunders is under the necessity of advancing the price of tiles by 2s 6d per thousand and of brick 2s 6d and that in consequence the former will be delivered at the works at 65s per thousand and the latter at 22s 6d per thousand. He continues to drive to Banff at 7d per hundred and any distance not exceeding 15 miles at 3d per mile for each hundred. Banff 04/03/1800.
02/02/1801 – Aberdeen Press and Journal – To be let, for such a number of years as can be agreed upon, and entered to at Whitsunday first. The farm of Blackpotts and Brick and Tile Work erected thereon, as presently possessed by the heirs of the deceased Mr Saunders, lying in the parish of Boindie, and on the sea coast of Banffshire, within two English miles of the town of Banff. The farm consists of 43 acres of arable land, and upwards of 20 acres of grass and pasture, of an excellent quality. This farm lies contagious to the farm of Upper Dallachy above advertised; both of which farms have a great command of the sea? ware and limestone within themselves; and within a hundred yards of the Brick and Tile Work there is a convenient harbour, at which vessels of a considerable burden may load and unload with the greatest safety. The farm and brickwork will be let separately or together, as may be agreed on. Offers may be given in to John Wilson at Cullen House by Cullen, betwixt and the end of February next, who will give any other information wanted. Cullen House, 29th February 1801.
Below – 30/11/1808 – Aberdeen Press and Journal – Blackpotts Farm and Blackpotts Brick and Tile Work for let. Apply to Mr Wilson or Alexander Stables, Cullen House.
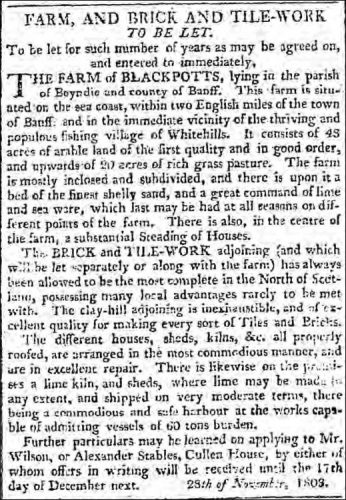
17/07/1811 – Aberdeen Press and Journal – Died at Limekilns, in the house of Mr John Reid; on the 8th July, James Webster, in the 85th year of his age. During his lifetime, he had been overseer of the tile-works at Cupar Fife, Glasgow, Prestonpans, and latterly at Black Pots, Banff. Piety to his maker and fidelity to his employers were ever conspicuous in the character of this good man.
24/10/1827 – Aberdeen Press and Journal – To brick and tile makers – to be let for such a number of years as may be agreed on, with entry at Martinmas first – The brickworks at Blackpotts near Banff. Offers will be received at Cullen House till 3rd November.
Below – 01/07/1829 – Aberdeen Press and Journal … Farmers and others sending to Blackpots for tiles and bricks where these articles are now manufactured on an extensive scale will find ample accommodation for their horses at the above stables …
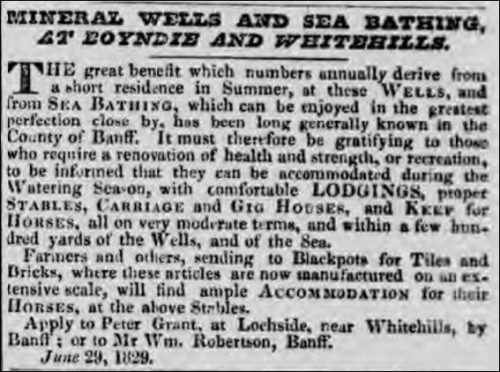
Below – 22/07/1846 – Aberdeen Press and Journal – Blackpots Brick and Tile Works – Messrs Alexr Duncan & Co beg to intimate to the public that their kilns are now in active operation …
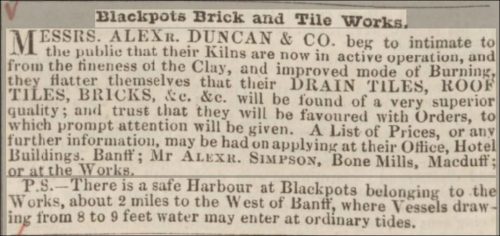
Below – 15/03/1848 – Aberdeen Press and Journal – Newly built schooner – maiden voyage – the vessel was loaded with drain tiles from Messrs Duncan & Co, Brick and Tile Works and sailed for Findhorn.
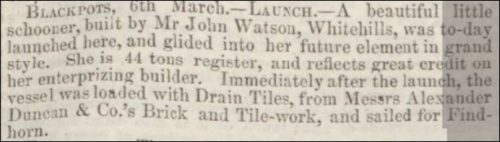
23/09/1848 – Witness Edinburgh – Rambles of a geologist … The Blackpots clay is of a dark bluish or greenish-grey colour and so adhesive that I now felt, when walking among it, after the softening rains of the previous night and morning, as if I had got into a bed of bird-lime. It is thinly charged with rolled pebbles, septaria and pieces of bituminous shale containing broken belemnites and sorely flattened ammonites that exist as thin films of white chalky lime … (Note – SBH – There is much more detail in the article).
Below – 06/08/1850 – Banffshire Journal – Wedding of Mr Duncan of Banff, one of the proprietors of the Blackpots Brick and Tile Works. Workmen were given a holiday to attend the wedding. John Stevenson, foreman also present.

06/01/1852 – Banffshire Journal and General Advertiser – Projected new road … A further projection of the road beyond Helens Haugh is also spoken about. It has been pointed out that, at a very little expense, the road could be made all the way to Whitehills – presenting, when completed, a marine promenade that would be perfectly unrivalled and affording the residents in Whitehills, the spirited conductors of the Blackpots brick and tile works and the Boyndie Mills a safe, easy and direct access to Banff for their produce and manufactures …
09/08/1859 -Banffshire Journal and General Advertiser – Seafield Estate Brick and Tile Work to Let. The Blackpots Brick and Tile Work will be let, on a lease, for such a number of years as may be agreed on, with entry a Martinmas first 1859. The work is situated about two miles from the town of Banff, and about half a mile from the fishing village of Whitehills. The Blackpots Harbour, built originally for the accommodation of the work, is in the immediate vicinity, and Stations of the Banff, Portsoy and Strathisla Railway are within two miles distance so that there is every facility for the conveyance, both by sea and land, of import and export materials. The bank of clay is extensive and of good quality, and there is sufficient supply of sand, both being quite close to the premises. The work has been established for upwards of 35 years, and a good trade carried on, which, with the encouragement now being given by the proprietors in the district for buildings and drainage on their estates, may be very much increased by a tenant of energy and capital. About 5 Acres of arable land and 10 of pasture are attached and will be let along with the work. Conditions of let, and all particulars, maybe learned on application to William G. Bryson, Factor, Cullen House, by whom offers to William G Bryson, Factor, Cullen House, by whom offers will be received till Friday, 30th September next; and Mr McNab the present manager, will show the premises and land attached. The present tenants are not to be offerers. Cullen House, 6th August.
04/12/1860 –
Banffshire Journal and General Advertiser – Launch at Banff – Launch at Banff.-On Tuesday last, there was launched from the building yard of Mr John Watson, a fine clipper smack of 37 tons register, ad which will class 7 years A 1 at Lloyds. The vessel is named ‘The Brick’ Her length is 56 feet keel; breadth of beam, 16 feet; depth of hold, 7 feet. She is expected to carry 70 tons ‘dead weight,’ and is intended to trade between Dunbar and London during the winter; carrying coals for Blackpots and Culloden tile-works during the summer. She is owned by Mr Wm. Brodie, brick and tile-maker. A considerable number of people collected to witness the launch of the vessel, which is no less creditable to the builder, that it promises to be remunerative to the owner. The vessel is commanded by Captain Sheils.
Below –1866 – Blackpots Tile Works, Whitehills, Banff.
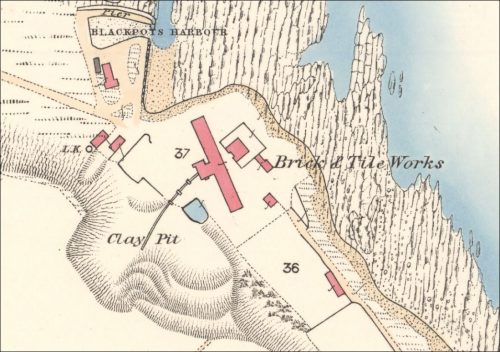
1867 – William Brodie, Brick and Tile Works, Whitehills, Banff, Banffshire and Dunbar.
1867 – 1869 – ScotlandsPlaces – Extensive manufactory of bricks, tiles, pipes &c. Situated on the seashore contiguous to “The Knock”, from which the clay is obtained.
Below – 07/06/1870 – Banffshire Journal and General Advertiser. Mr Brodie of Battlebent, the energetic owner of extensive tile and brickworks both in the north and south country and lessee of the works of that nature at Blackpotts near Banff has just had a fine little screw steamer built for service in connection with the works …
25/09/1871 – Shipping and Mercantile Gazette – 20th September – The Brick, Wilson (Captain), from Blyth (Northumbria) for Blackpots.
Below –
20/02/1877 – Banffshire Journal – Claims to be lodged in respect of the late William Brodie of Battleblent, Dunbar, lessee of Blackpot Brick and Tile Works. James McNab manager.
Below –
08/01/1878 – Banffshire Journal – Alexander Brodie, Broxburn, Dunbar takes over Blackpots Brick and Tile Works from his late father, William Brodie.
22/02/1881 – Banffshire Journal – Blackpots Brick and Tile Works, near Banff. On hand a large stock of bricks and drain pipes – all sizes – 07/02/1881
Below –
01/10/1881 – Aberdeen Press and Journal – Accident at Blackpots Brick and Tile Works – James Riddell requires an arm to be amputated.
28/03/1882 – Banffshire Journal – Mr Brodie of Broxburn, tenant of the Blackpots Brick and Tile Works near Banff has been again elected chairman of the Dunbar Burgh School Board.
Below –
23/12/1884 – Banffshire Journal – Blackpots advert re account collection.
Below –
06/10/1885 – Banffshire Journal – Blackpots advert. James McNab Manager.
1886 –
Alexander Brodie (& pottery ware), Whitehills, Banff. James McNab Manager.
18/02/1888 – Aberdeen People’s Journal – Alleged savage assault on policemen – William Brodie, brick and tile worker, Whitehills, John Kilgour, china merchant’s assistant, Banff, and David Bell, ostler, accused of an offence against the Prevention of Crime Act. 1871. by severely assaulting two police constables in the execution of their duty, emitted declarations before Sheriff Hamilton Grierson on the 9th inst and were subsequently liberated finding bail for £5 each.
17/09/1889 – Northern Ensign and Weekly Gazette – Alexander Sinclair, auctioneer, Wick would invite the attention of agriculturalists to his present supplies of … Brodies’ drain tiles of superior manufacture 2 in. to 6 in. diameter …
11/03/1890 – Aberdeen Press and Journal – Coursing. Banff fox terrier club. Yesterday the second match for 1890 in connection with the club was held on a field on the farm of Sandyhill near Banff, kindly lent by the tenant, Nr William Simpson … All aged stakes first round – Mr William Brodie’s ‘Brick Dust’ beat Mr R. G. Sheriff’s ‘Ben’.
Below –
21/02/1893 – Banffshire Journal – Testimonial to James McNab.
1898 – Alex Brodie – Brick and Tile Works, Boyndie, (Blackpots) Banffshire.
Below – 09/11/1898 – Aberdeen Press and Journal – Alexander Brodie taken to court re the death of an employee, John Mackie a carter, but the case was dismissed.
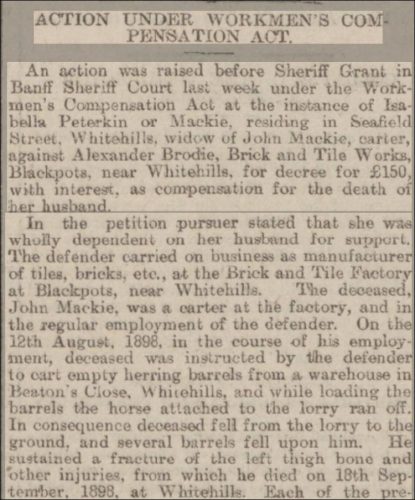
.

22/01/1901 – Banffshire Journal – Blackpots advert – Blackpots Tileworks, Banff – on hand, bricks, drain pipes, flower pots, terracotta and fire clay goods of the best quality – Alex Brodie.
1903 – Alexander Brodie, Brick & Tile Maker,( & pottery ware), Whitehills, Banff.
10/11/1904 – Northern Times – Agricultural drain pipes, bricks etc. Large stock on hand. Delivery by rail or boat. Brodie, Blackpots Tileworks, Banff.
19/12/1904 – Aberdeen Press and Journal- Whitehills … This week a sloop was in the harbour with coals for Mr Brodie, Blackpots and left with bricks and tiles for Skibo Castle…
07/03/1905 – Inverness Courier – Agricultural drain pipes, bricks etc, flowerpots and other terracotta goods. Delivery by rail or boat. Blackpots Tileworks, Banff.
31/07/1906 – Banffshire Journal – Agricultural drain pipes, bricks etc, large stock on hand. Delivery by traction, rail or boat. Prices on application. Alexr Brodie, Blackpots Tileworks, Banff.
03/05/1910 – Banffshire Journal – Farm servant had 14 teeth extracted and sued for damaged that occurred during the course of this extraction. The ‘dentist’ was William Brodie, Manager of the Blackpots Brick and Tile Works (Son of Alexander Brodie) … William Brodie stated that he pulled teeth for children or anyone in the district who was troubled with bad teeth and made this his hobby. The Sheriff stated that it was a somewhat peculiar hobby! (24/05/1910 – the Sheriffs verdict – case not proven on either side. No expenses awarded to either).
1912 1913 – Alex Brodie – Blackpots Brick and Tile Works, Whitehills, Banff, Aberdeenshire.
Below – 17/12/1926 – Aberdeen Press and Journal – Advert for the Blackpots Brick and Tile Works. Henry Napier.

09/06/1934 – Aberdeen Press and Journal – New Companies – Henry James Napier, Brick and Tile Manufacturer, Black Pots, Whitehills, Banff.
03/04/1937 – William Brodie, son of Alex Brodie, Brick and Tile Works, Blackpots dies. Previously assisted his father at the brickworks and then created a ‘considerable practice in dentistry’ – (Note – this seems remarkable following the newspaper article dated 10/11/1904).
22/07/1976 – Aberdeen Press and Journal – article on the Blackpots Brick and Tile Works site with regards to its future use. Land valued at £35, 000 and currently owned by the Earl of Seafield.
1978 – Works demolished after a bid to save it by preservationists. Work on the caravan site begins. The newspaper states the brickworks were 200 years old.
Below – 2 photos taken in 2015 of the foreshore in front of the Blackpots Tileworks, Whitehills, Banff – a debris layer of old tiles etc can be seen with 3 feet of soil leading to the verge and road above.
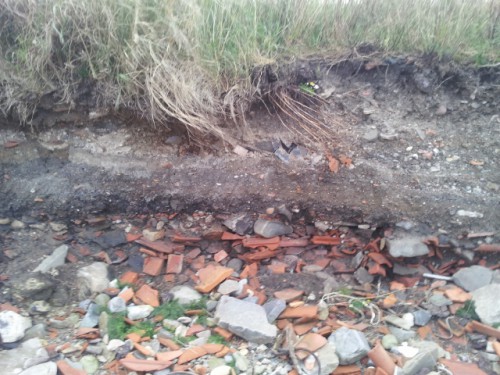
.
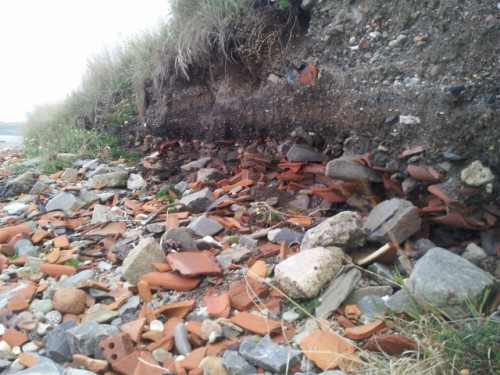
***********************************
The following firebricks were found on the beach amongst the clay tile debris – Forth, Preston Grange, Glen and H.Carr & Co
******************************
The following clay products were found in beach debris at Blackpots Tileworks, Whitehills, Banff and are presumed to be a product of the same.
Measurements in MM are approximate due to the irregularity of the product shape and sea erosion.
Top left – Cored brick – 20 holes – 80mm x 105mm 230 mm – This has significant kiln firing damage and has blown out on both sides however it was covered in mortar so a use for it was found.
Bottom left – This is perfect and well-fired.
Top right – This is covered in whitewash and measures 75mm x 110mm x 230mm.
Bottom right – This is an undersized brick. It appears to have been manufactured thus. 65mm x 110mm x 230mm.
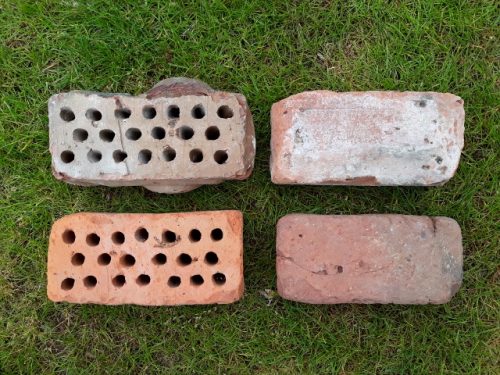
.
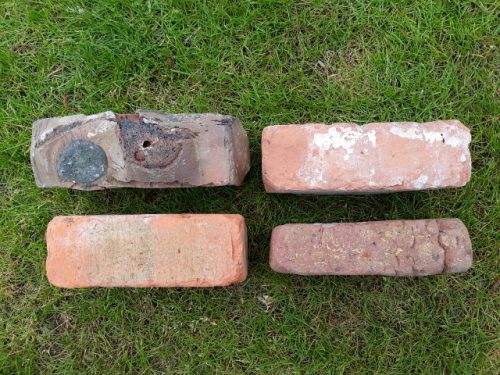
Below – The following product appears to be a ‘brick drain’ – 73mm x 105mm x 230mm with a 43mm x 80mm hole running from end to end.
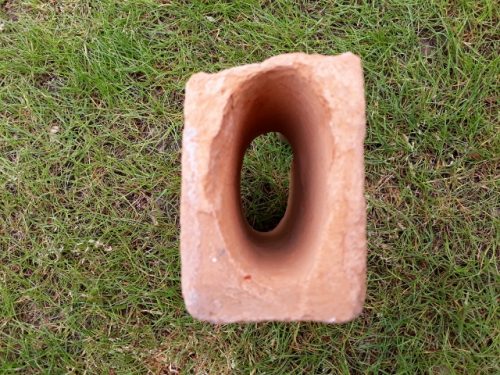
.
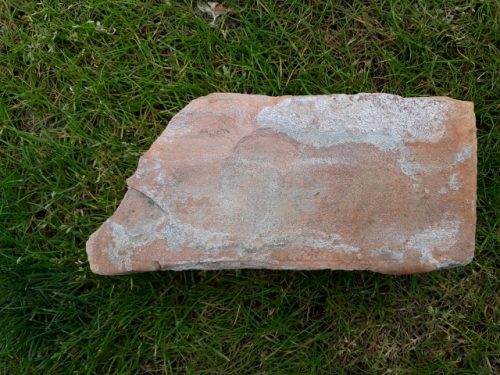
Below – D shaped drainage tile. Base 60mm. Tile diam 70mm round.
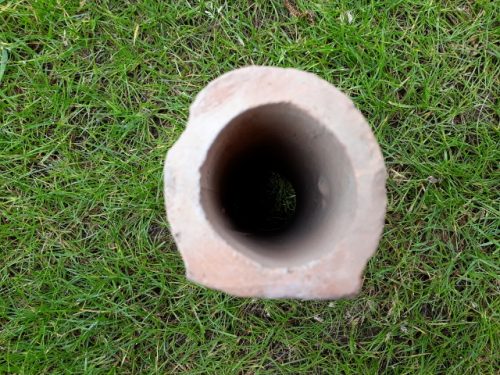
.
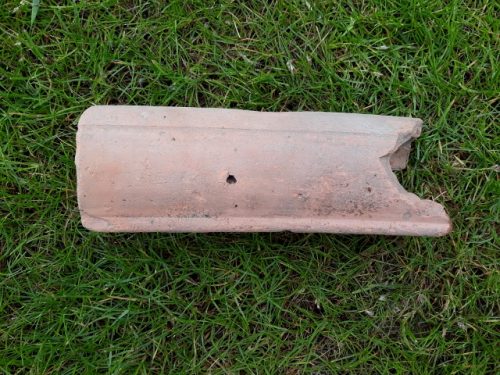
Below – Round drainage tiles x 2 – 60mm diam and 70mm diam. They are of unknown length as both are broken.
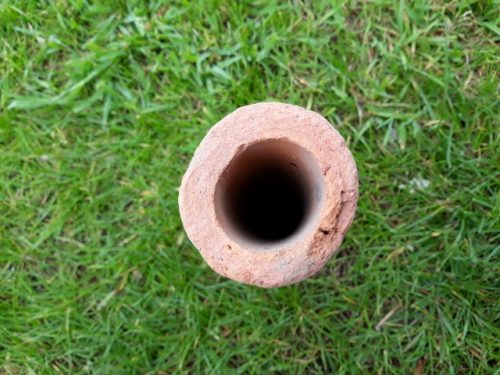
.
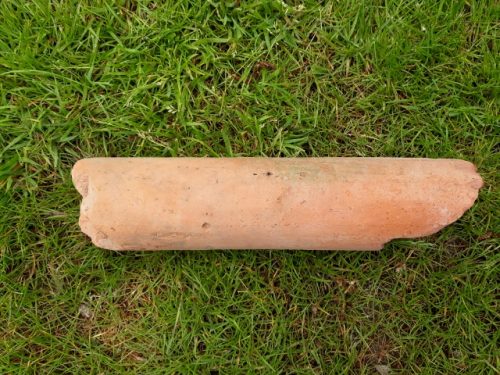
.
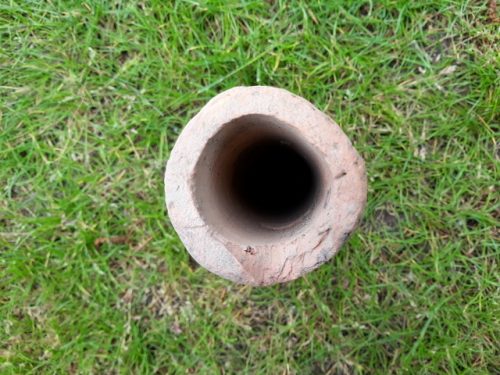
.
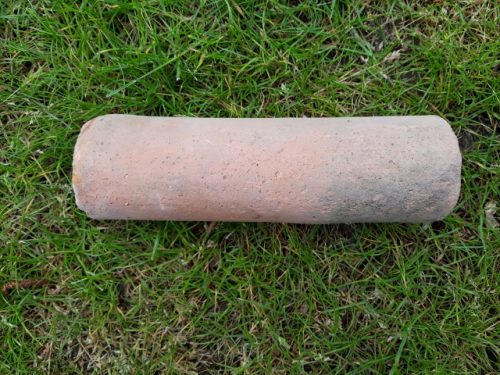
Below – D Shaped drainage tile – approx 112mm diam – left in situ as sticking out of debris banking.
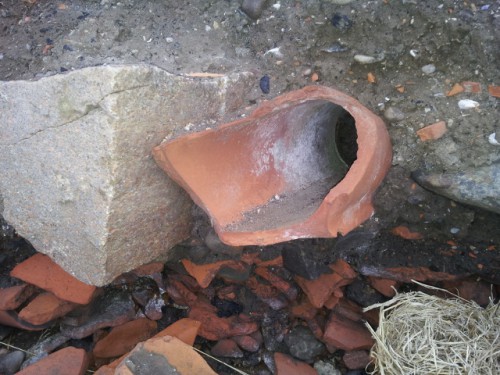
Below – An example of a blown drainage tile 70mm diam.
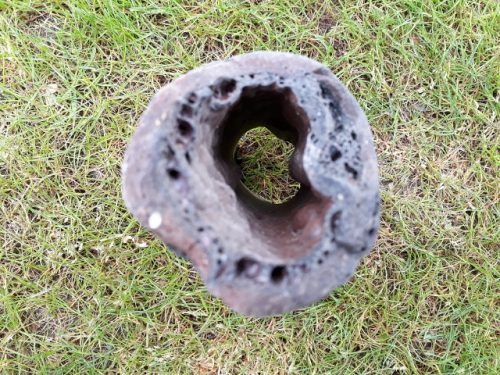
.

Below – The following land drains were found in 2018 by Ian Suddaby during ground excavations in and around Blackpotts. They were found within 1 mile of the works and are believed to be products of the same.
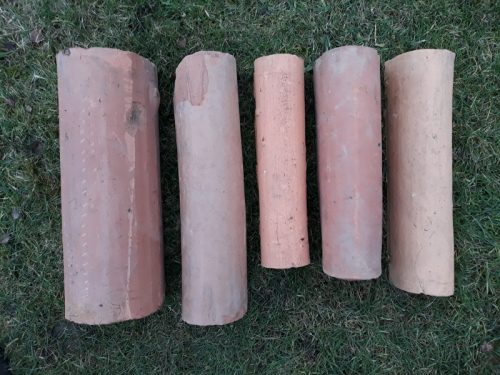
.
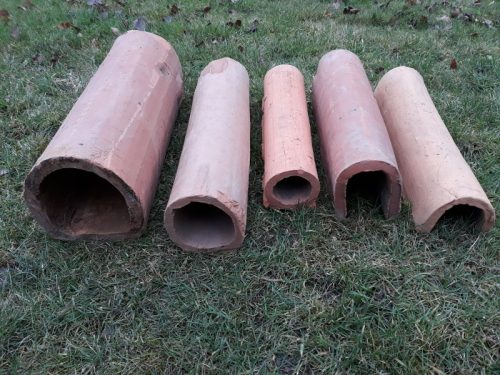
.
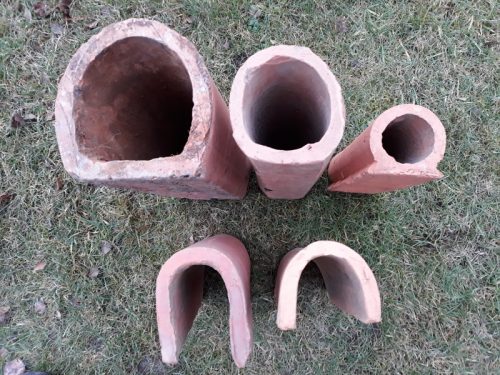