This pamphlet describes the range of refractories manufactured by James Dougall & Sons Limited from fireclay and ganister raw materials coming from their own mines. The whole process of
manufacture from the winning of the raw materials through the clay preparation, moulding and firing, to the departure of the finished product is consequently under the direct control of the management aided by the laboratory staff.
Separate pamphlets, which are also available, describe the various Dougalene refractory cements and the range of Aludo (high alumina) and Sicardo (silicon carbide) refractories which are also
manufactured and supplied from the Company’s works at Bonnybridge.
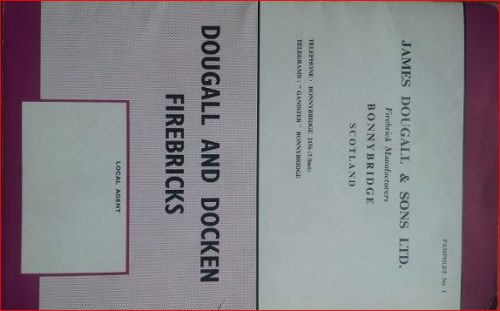
.

Purchaser’s guide
Place your orders early
In order to meet customers’ demands with as little delay as possible, comprehensive stocks are maintained in the standard sizes based on
the Standard Sizes Booklet issued by the Scottish Employers’ Council for the Clay Industries. It is recommended that these standard sizes should be used wherever possible.
Stocks cannot always be available in every size and quality. Fire-bricks take two to seven weeks to manufacture and if made in a hurry to meet an urgent delivery date, more are liable to be defective. Disappointment can also sometimes be caused if a few bricks are found to be defective after burning and time has not been allowed for the manufacturer to remake.
Technical enquiries are always welcome.
Dougall and Docken are only two of a wide range of qualities produced. A wide range of intricate shapes are regularly manufactured and, in some cases, designs which are exclusive to the Company can be suggested. A good firebrick of the wrong quality or design can prove to be a bad fire-brick in service.
A well-equipped research laboratory is maintained at Bonnybridge. Data from many years of research and study of users’ problems can often be of assistance.
The Sales Department gladly advises on transport problems
Both for home and export orders problems can arise as to the best methods of packing and routing. Suggestions can sometimes be made from the background of the Company’s experience which can reduce transport costs or eliminate damage in transit.
Shipments
Shipments can be most cheaply effected from Glasgow, Leith or Grangemouth, the Company’s works being situated within easy reach of these three ports. Clay for export is supplied packed in paper or jute bags according to customers’ preference. Firebricks can be shipped loose or packed. It is recommended that special shapes and standards in the more expensive qualities should be packed for export.
Home deliveries
Purchases made in minimum quantities of 6 tons avoid charges for extra carriage. Wagons containing clay are despatched sheeted, but when customers require wagons containing bricks only to be sheeted, this should be specially stated in their order. Firebricks can be supplied on returnable pallets without extra charge.
Methods of testing
Refractoriness: A test by Seger cone of the temperature at which the material commences to melt when heated at a standard rate in an oxidising atmosphere.
Refractoriness-under- Load: A test to determine the temperature at which a firebrick commences to lose shape when heated at a standard rate under a definite load in an oxidising atmosphere. The usual standard load for this test is 2 kilograms per square centimetre (28.45 lbs. per square inch).
Permanent Linear Change: A standard temperature (usually 1410 C.) is taken and the brick sample is maintained at this temperature for 2 hours. The brick is measured before and after heating and the difference in size expressed as a percentage of after-contraction, or after-expansion is the permanent linear change.
Apparent Porosity: A test to ascertain the volume of air spaces which can be penetrated by a liquid. The result is expressed as a percentage of the total volume.
Cold Crushing Strength: A pressure test on a rectangular sample by which the weight is added at an agreed rate until the test piece fails. The load applied to the top face of the sample at the time of failure is expressed in lbs. per square inch.
Other data: concerning firebricks is sometimes asked for, such as:
Reversible Thermal Expansion: Rate of expansion while the sample is being heated.
True Specific Gravity: Weight of the material in relation to the weight of water having a volume equal to the volume of the material plus the volume of the sealed pores.
Spalling: The resistance of the material to cracking under rapid temperature fluctuations.
Slag Attack: The resistance of the material to the penetration of slag at high temperatures.
Permeability: The resistance of the material at normal temperatures to the penetration of gases.
For some of these tests, there is no standard method of testing and buyers should not make the comparison on manufacturers’ data without first ensuring that the same method of testing has been applied in each case.
Reference Data
Two to three cwts. of fireclay should suffice for building 1,000 firebricks.
Approximately 19 cub. Ft. of bricks weigh 1 ton or 1016 kilos.
One English ton weighs 1016 kilos. A metric ton is 1000 kilos.
One linear inch is equal to 25.4 millimetres.
To convert Fahrenheit to Centigrade: Deduct 32, multiply result by 5, and and divide by 9.
To convert Centigrade to Fahrenheit: Multiply by 9, divide by 5 add 32 to the result.
Seger cones are used to determine the temperatures of the softening points of clay and bricks. For Seger cone values see chart.
English linear measure: 12 inches=1 ft. 3ft.=1 yard.
English square measure: 144sq. inches=1 sq. ft. 9sq. ft.=1 sq. yard.
English cubic measure: 1728 cub. Inches=1 cub. Ft. 27 cub. Ft.=1 cub. Yard.
English weights: 112 pounds (lb.)=1 hundredweight (cwt.). 20 cwts = 1 English ton.
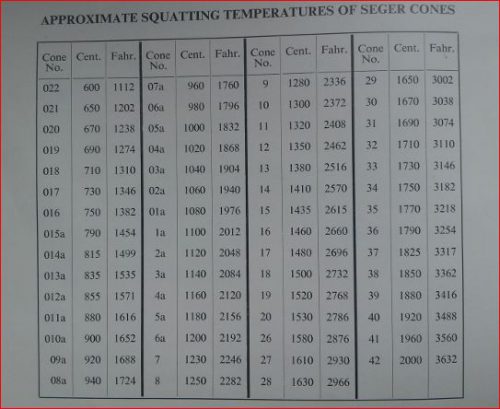
J.D Semi – silica
This firebrick is manufactured from the well-known Bonnybridge ganisters which are obtained from the Company’s own mines. Although less refractory than the other firebricks produced by the
Company, J.D. has a greater volume stability than the ordinary type of firebrick under heavy loads provided the temperature is not excessive. It also has the advantage for some purposes of a slightly higher thermal conductivity.
J.D. is not normally recommended for use at working temperatures in excess of 1400 C. It is especially favoured for use in many positions in gaswork and coke oven installations, but also has other
industrial applications. Although less refractory that the clay bonded silicious firebricks containing about 90% silica (J.D. contains about 78/80% silica), J.D. does not suffer from the permanent
expansion which can be expected from products containing a higher percentage of silica.
While a good quality firebrick will tend to contract under heavy load conditions in service and a good quality silica brick will expand, J.D. will maintain its volume size provided the temperature is not excessive. No expansion joints are required other than those normally used for an ordinary firebrick construction.
J.D. also has a greater resistance to thermal shock at low temperatures than bricks which contain a higher percentage of silica, thus reducing the risk of damage during the heating up and cooling
of a furnace structure.
Dougall and Dougall A
Both the Dougall and Dougall A qualities are in the range of firebricks containing between 35% and 40% alumina. The reason why two brands are offered in this range is given below in order to assist purchasers in their choice for their particular requirements.
It will be noted in the technical data given later in this pamphlet that the difference between Dougall and Dougall A in analysis and refractory properties is not very material.
Dougall A is slightly the more expensive of the two qualities. Its use is recommended where extreme accuracy of size and shape is required in standard sizes used for the construction of hearths, walls or arches. In order to avoid unnecessary duplication of stocks of the larger standard sizes of squares and tapers 9” x 6”, 12” x 6” and 13 ½” x 6” are manufactured by the Dougall A process and branded Dougall. Dougall A is manufactured along with the Docken quality in an entirely separate modern works which is designed in its clay preparing methods, dry-press moulding and tunnel kiln burning to ensure the production of the highest possible quality of standard products. The plant is fully mechanised so that the bricks are normally only handled twice; firstly, when setting the brick from the machines direct onto the kiln cars; and, secondly, when taking the firebricks from the kiln cars on to the pallettes on which they are loaded out to the customer. This ensures an almost complete freedom from chipping and other damage.
Dougall is the cheapest firebricks available in the Dougall range of refractories. Either Dougall or Dougall A can be found serving a useful purpose in almost every type of industrial furnace. Dougall standard shapes are manufactured stiff-plastic or dry pressed. They have an excellent resistance to high temperatures, thermal shock and slag attack and the high standard insisted upon in manufacture ensures the close uniformity in quality, size and shape. A rigid control in the selection of the raw materials, the moulding process and the firing is constantly maintained.
An important feature in production both of Dougall and Dougall A is the large variety of special shapes of all types and assizes which are regularly supplied to customers’ requirements.
Docken and Aludo 4
Both Docken and Aludo 4 are in the range of high alumina firebricks containing between 40% and 44% alumina. An explanation is given below why two brands are offered so that purchasers can make the best choice for their particular requirements.
It will be noted in the technical data given later in the pamphlet that there is little difference in analysis between Docken and Aludo 4, but the latter has certain advantages in physical properties.
Docken is a competitively priced high alumina firebrick which is manufactured from specially selected raw materials coming from a separate mine also under the Company’s control. The standard shapes are normally dry pressed and tunnel kiln fired in the same modern works as the Dougall A quality. Special shapes are usually manufactured plastic or plastic-repressed are fitted in a specially designed producer gas-fired chamber kiln which provides an exceptionally high standard of firing control.
Aludo 4 is a more expensive variation of the Docken quality with a greater density and a greater resistance to thermal shock due to the special methods of clay preparation and manufacture. This method is similar to that employed of the other Aludo refractories containing 50% alumina and upwards which are made from imported raw materials and are described in a separate pamphlet.
Aludo 4 will normally justify its selection in preference to Docken where conditions of thermal shock or slag attack are too severe for an adequate life with Docken, but not sufficiently severe to justify the use of the more expensive higher alumina Aludo qualities manufactured from imported raw materials. The special method of manufacture employed for Aludo 4 ensures a quite remarkable accuracy of size and shape and a considerable variety of special shapes are manufactured in this quality by the same process.
It is noteworthy, with the more exacting conditions in modern furnaces, that many customers both at home and abroad were previously satisfied with Dougall or Dougall A qualities only, but are now preferring the use of Docken or Aludo 4 in selected positions.
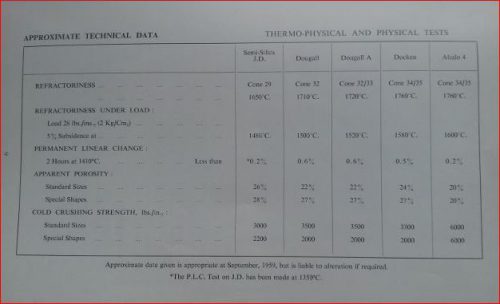
.
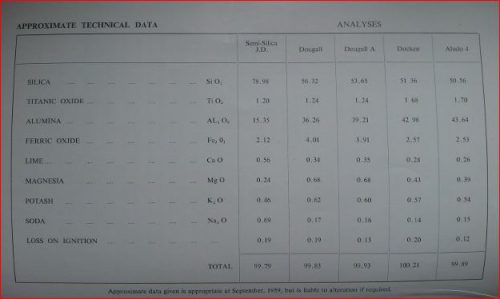
Industrial applications
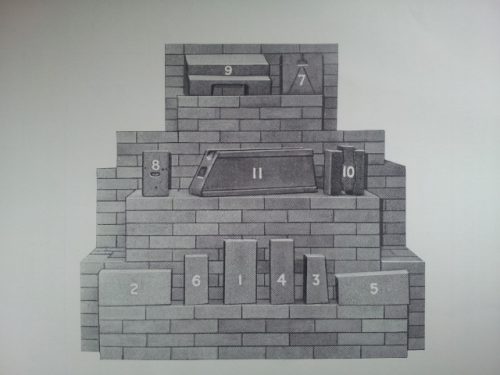
Steelmaking
The 12” x 6” x 3” standard Docken quality firebrick. No.2 in the photograph is for service as a regenerator brick in the top courses of the checkers in an open hearth furnace. Many steelworks give preference to our Docken quality for their exacting conditions. The steelworks is the largest consuming industry for firebricks and many other sizes in the full Dougall range of qualities are supplied for use also in the ladles, soaking pits, reheating furnaces, ect., in steelworks both at home and overseas.
Iron making
No steel can be made without iron. No. 1 in the photograph is a 13 ½” x 6” x 3” square brick in Dougall quality from the standard sizes of firebricks which are usually preferred in Great Britain for the lining of blast surfaces. Various qualities are available for the different requirements in blast furnaces and hot blast stoves and the Dougall record of successful service is second to none. In particular, the providing of a product capable of adequate resistance to carbon monoxide attack and abrasion in the shaft of a blast furnace can only be obtained from an extensive manufacturing experience and study of the problems concerned.
Iron and non-ferrous foundries
No. 3 in the photograph is a normal 9” x 4 ½” x 3” taper which is popularly used for the lining of cupola furnaces, although larger blocks can be supplied, such as the Dougall V Cupola which eliminates straight through joints as well as reducing their number. The exacting requirements for the lining of cupola furnace are admirably met by the standard Dougall quality which has been proved to be capable of giving a long life and the minimum of wear, particularly in the zone immediately above the tuyeres where the greatest wear takes place.
Two excellent qualities of fettling material for the patching of cupolas are also supplied wet prepared ready for use in the Dougall “foundry mixture”, and the more expensive No. 10 Dougalene for use in cupolas where the conditions are more severe. Where the patching has to be of a greater thickness than two or three inches, fireclay splits are also supplied to be used along with the patching material.
Glass Making
The Docken standard brick, No. 4 in the photograph, is for service as a regenerator brick in a glass tank furnace. In such furnaces the size of the brick used and the quality can vary considerably with the design of the furnace and the type of glass melted, but a Docken firebrick or a more high alumina product such as the Aludo 6 is usually preferred for the more exacting positions. The Dougall and Docken firebricks are also used for the construction of the regenerator chambers. J.D. quality shapes are giving excellent service for the jack arch block.
Lime and Cement Kilns
The 13 ½” x 6” x 3” taper in Docken quality, No 5 in the photograph, is popularly used in modern lime kilns of the shaft type where the method of construction and size of brick used is similar to that employed for building blast furnaces. A brick of good abrasion resistance as well as with good resistance to chemical attack is required. Docken is usually preferred in the high temperature zones and Dougall where the temperatures are lower. Both qualities are also used in selected positions in rotary lime and cement kilns.
Oil Industry
The 9” x 4 ½” x 2 ½” standard firebrick in Dougall A quality, No. 6 in the photograph, is one of many sizes of standard and special shapes which are regularly supplied in various qualities to oil refineries, both at home and abroad. For the varied requirements in oil refining furnaces a firebrick in the 35% to 40% alumina group will usually meet the refractory requirements. It is
essential, however, that a well-fired refractory of good shape and size is employed and the Company have a wide experience in the supply of the correct refractories for oil refining installations. In oil-fired installations also, for burner blocks and combustion chambers, the Dougall and Docken refractories are giving notable service.
Water Tube Boilers
No. 7 in the photograph is one of may designs of suspended arch blocks which are used for the ignition arch in a modern water tube boiler. This type of flat arch is frequently preferred to the radius arch in many types of industrial furnaces, the bricks hanging from a suitable steel structure instead of being dependent on the key of the circular arch to retain their position and carry any weight above them. For such suspended arches great accuracy in size and shape is essential and long experience in their manufacture ensures satisfactory results with the Dougall products. In water tube boilers, Lancashire boilers and other types, other special shapes and standard bricks are required for the side walls, boiler seating blocks and flue covers, and the Company have a wide experience in the supply of all such products.
Marine Boilers
The Company are one of the principal suppliers of the refractories for use in marine boilers for the British Navy, and for naval requirements in other countries, as well as supplying for Merchant shipping requirements throughout the world. No 8 in the photograph is a special shape in Dougall quality for use in the side wall of an oil-fired marine boiler, and is a type which is suspended by a bolt into the brickwork which is secured against the outer casing. Both for the boiler walls and the burners themselves in oil-fired marine boilers, a large range of shapes are supplied in different qualities to meet the varied requirements.
Gas Industry
No. 9 in the photograph is a special shape in Dougall quality, and is one of a large variety of sizes which are used to construct vertical gas retorts. This particular brick is in Dougall quality, but J.D. and Docken qualities are also supplied to suit particular conditions. Also in horizontal gas retort installations all three qualities are in regular use both as special shapes and standard firebricks.
Coke Ovens
No. 10 in the photograph is in J.D. Semi-Silica quality and is a typical shape used for the construction of a coke oven wall. It is customary to use the J.D. quality in preference to silica in the wider types of ovens such as those generally used for the manufacture of foundry coke, and with the J.D. quality a normal life of 20 years for the coke oven walls is quite usual. The exceptional volume stability of the J.D. brick ensures tight joints without gas leakage during the whole life of the coke oven. In coke oven installations working with narrower chambers and high temperatures the ore refractory silica bricks are required for the coke oven walls, but both J.D. and Dougall quality still play their part in the structures below sole level and in the tops of the ovens.
Ceramic Industry
No. 11 in the photograph is one of many types of special shapes supplied to the Ceramic industry. This particular shape is for use immediately below the deck of a kiln car which passes through a gas-fired tunnel kiln firing sanitary waste. Owing to the rapid firing cycle, this particular shape has to withstand the heat and load conditions without deformation. The Company along with their
associated Company, the Diamond Clay Co. Ltd., Stoke-On- Trent, have an exceptionally wide experience in the supply of all types of refractories for the very varied requirements in the Ceramic industry. There are few manufacturers of fine ceramics in Britain who do not use some of the Dougall or Diamond Clay Co. products in their kilns and other furnaces, and almost every type of refractory required in the industry can be supplied as an already proved product capable of giving the maximum service.
Export
Although no particular brick can be selected as an example of the service which the Company provides for customers abroad, a substantial percentage of their output is being regularly delivered to many countries in all the continents throughout the world. In many such countries local agents and stockists can provide additional services and prompt attention is always given to enquiries and
requests for technical information from customers abroad. Goods are despatched expeditiously, suitably packed and routed by the cheapest method available. Bonnybridge is geographically well placed to provide cheap f.o.b. prices for Glasgow and Grangemouth to both of which ports the costs of transport are small.
It has only been possible to describe some of the requirements which the Company supplies to certain industries. Both in the industries mentioned and others such as the smelting industry and the aluminium industry, many others are found for the Dougall firebricks, and the extensive Research Laboratories of the Company are at their Customer’s disposal to study and advise on all types of problems concerning the most suitable refractory to use for specific conditions. These facilities backed up by over 75 years of manufacturing experience are always at the customer’s service.
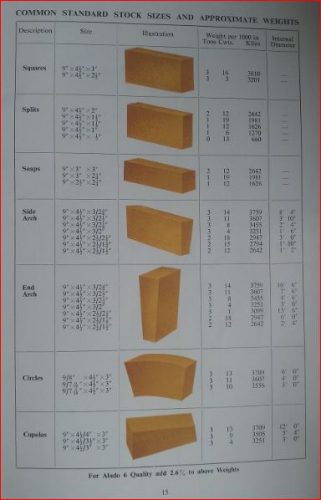
.
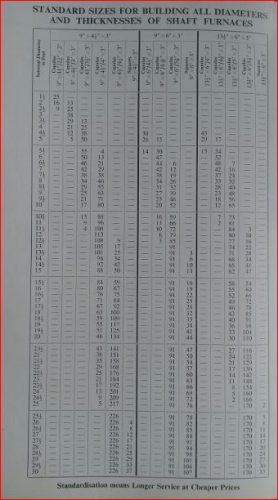